Liquid and Fluid Level Sensors and Gauging
Liquid And Fluid Level Sensors And Gauging
Knowing the amount of liquid or fluid inside a tank or other vessel is an important variable in any process to maximize process efficiency and help prevent overflows and running dry. This variable is what operators call level. This can be something as simple as a full or empty signal, or it can be a continuous level measurement to track how the level inside changes during a process.
To measure liquid level, there are a number of different technologies used ranging from the simple to very complex. VEGA uses liquid and fluid level sensors, transmitters, and switches with seven different technologies to measure level in a multitude of different applications across at least a dozen key industries.
Liquid Level Sensor Technologies
The technologies at VEGA are: through air radar, guided wave radar, pressure, vibration, capacitance, radiometric, and ultrasonic. These different measuring methods detect level and convert that level into an electronic signal to be displayed directly at the vessel or incorporated into a process control or management system. Each of these technologies has their pros, cons, and different price points. It comes down to what liquid is being measured, what is happening inside the vessel, and the vessel’s construction.Radar
How it works
Radar sensors send microwave signals toward the liquid being measured from above. The surface of the liquid below reflects the signals back in the direction of the antenna system. The instrument uses the time of flight for the microwave signals to determine a distance to the product surface, and then calculates a level inside using the known height of the tank or vessel.
Non-Contact Liquid Level Detection
Non-contact liquid level detection sensors using radar technology are trusted to measure liquids with accuracy and reliability. The VEGAPULS series of radars specializes in continuous liquid level measurement.
VEGA Radar Sensors
VEGA’s radar sensors operate under three different frequencies: C-Band (6.3 GHz), K-Band (26 GHz), and W-Band (75-85 GHz). All three are used for continuous non-contact level measurement for all kind of liquids, even under high pressure and extreme temperatures. They can be used in simple or aggressive liquids, and are suitable for applications with stringent hygiene requirements.
Advantages
- Non-contact liquid level measurement with high accuracy
- Measurement not affected by temperature, pressure, foam, or condensation
- User-friendly adjustment saves time
- Maintenance-free operation through non-contact measuring principle
Related products
Related applications
Storage and buffer tanks
Level measurement and point level detection in small storage and buffer tanks
Storage and buffer tanks enable a reliable material supply for various ongoing processes. The plant operators need to have exact level data from these tanks at all times to ensure timely replenishment and facilitate continuous production. In addition, the measured values form the basis of the statistical consumption analysis for validation and quality monitoring.
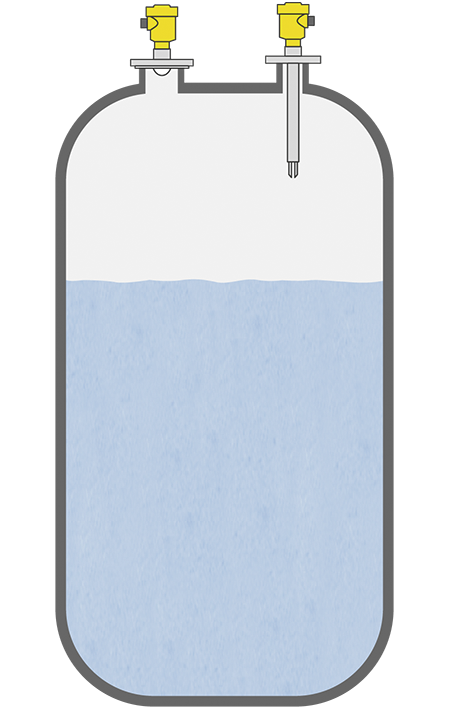
Reliable
Reliable protection against overfilling
Cost effective
Independent of product and process characteristics
User friendly
Simple to set up with maintenance-free operation
Finished product tanks
Level measurement and point level detection of finished product tanks
Reliable level measurement of crude and bulk liquids storage tanks in a refinery is necessary for inventory management and overspill protection. Multiple measurement devices can fit into a single process fitting.
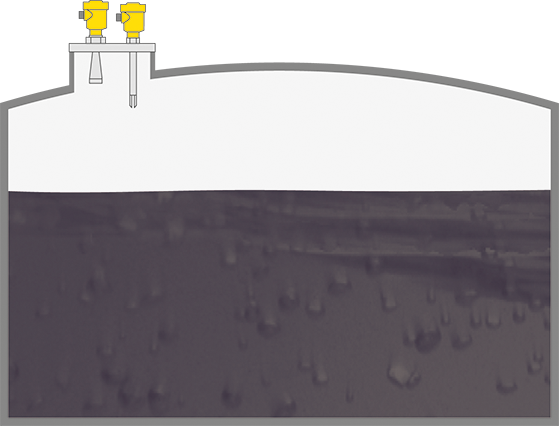
Reliable
Redundant measurement ensures a high degree of safety
Cost effective
Self-monitoring reduces maintenance costs
User friendly
Easy installation and setup
Pumping station
Level control in a pumping station
Wastewater from households and businesses, together with surface water, is carried to the wastewater treatment plant via an extensive sewer network. If the natural gradient is not steep enough, numerous pumping stations are required to create a sufficient height difference. The level measurement in the inlet shaft is used for cost-effective control of the pumps.
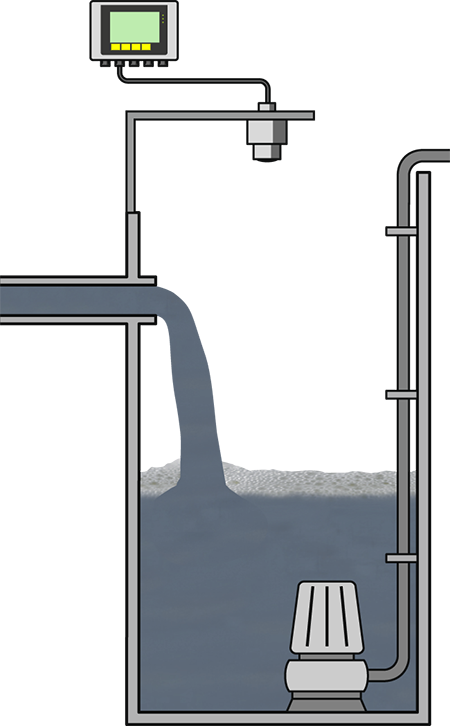
Reliable
Reliable measurement of the level
Cost effective
Pump switching ensures optimal operating times
User friendly
Maintenance-free, trouble-free operation
How it works
Guided wave radar sensors use time domain reflectometry to measure level. A cable or rod probe is mounted on top of the tank or vessel, and a low amplitude, high-frequency microwave pulse is sent down the probe to be reflected by the surface of the liquid or fluid. Once the pulse reaches the surface, a portion of the signal bounces back, and the amount of time it takes for the pulse to be transmitted and returned determines the level inside the tank or vessel. Some calibration is required dependent on the liquid’s conductivity.
VEGA Guided Wave Radar
The VEGAFLEX 80 Series can measure a range of liquids even in the presence of steam, buildup, foam, and condensation. Three different probe options – cable, rod, or coax – ensure an accurate measurement for a range of liquids and fluids being measured. A selection of sensors gives operators the ability to make simple measurements as well as measuring aggressive liquids and liquids under extreme pressure or temperature conditions.
Advantages
- Comprehensive diagnostic options ensure low-maintenance operation
- Shortenable probes enable simple standardization and maximum flexibility
- Measurements not affected by steam, pressure and temperature fluctuations, foam, noise, buildup, and condensation
- Can take measurements in standpipes
Related products
Related applications
Tanks for solvents
Level measurement, point level and pressure measurement in the storage and transfer of solvents
Low viscosity solvents can degrade many types of plastics. This places increased demands on the process instrumentation. A separate level detection system is required for protection against overfilling. It increases plant safety and ensures protection of human health and the environment.
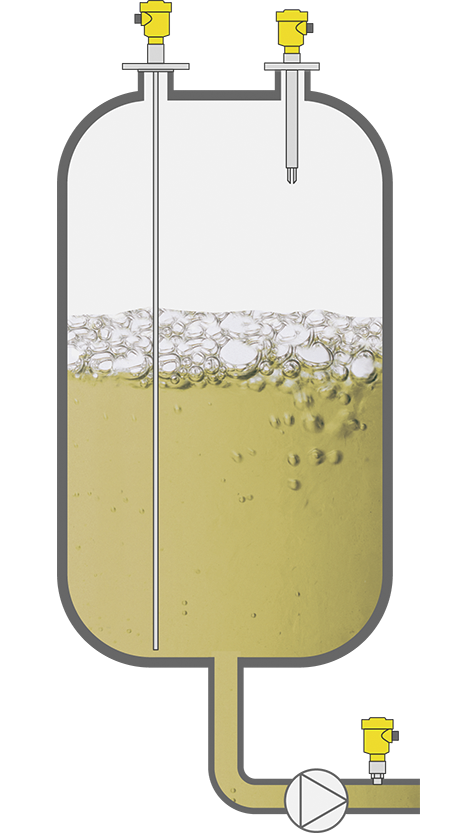
Reliable
Reliable protection against overfilling
Cost effective
Independent of product and process characteristics
User friendly
Simple to set up and maintenance-free operation
Oil separators
Level and pressure measurement in an oil separator
The separator vessel contains a mixture of crude oil, gas, water and sand extracted from the subsea well. Precise monitoring of these multiple separation interfaces and emulsions play a vital role in ensuring the quality of the oil separator for separation. Exact control of interfaces, level and pressure allows optimum utilization of the oil separator and increases the effectiveness of the entire asset.
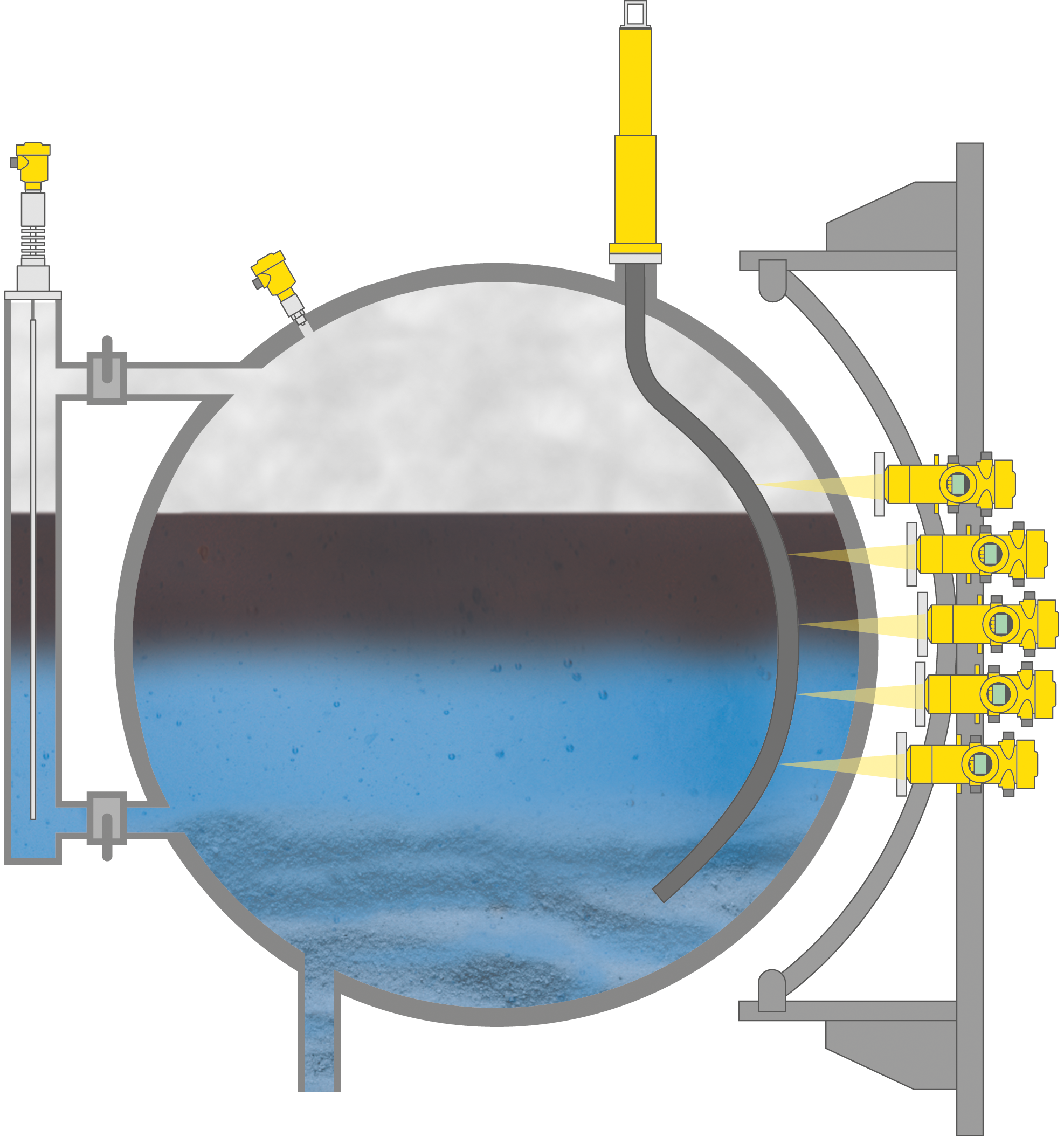
Reliable
Measurement results are unaffected by process conditions
Cost effective
Efficient operation and high oil quality
User friendly
Maintenance-free operation
High temperature separators
Level and interface measurement and point level detection in high temperature separators
Exact interface measurement in high temperature separators is important for ensuring the quality of the separation process. Continuous control of the interface between oil and water ensures that oil is not inadvertently withdrawn instead of water. This saves costs and increases the efficiency of the plant. A vibrating level switch serves as an additional overfill protection mechanism.
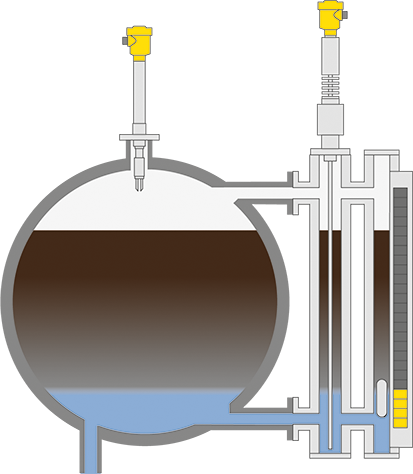
Reliable
Redundant measurement for highest safety standards
Cost effective
Maintenance-free operation
User friendly
Easy installation
How it works
Hydrostatic pressure refers to the pressure generated on a cell from the mass of the liquid above it. As level increases inside a tank or vessel, the hydrostatic pressure increases proportionally. Thus, the higher the hydrostatic pressure, the higher the liquid level measurement. To get an accurate level measurement from a pressure transmitter, the density of the fluid must remain fairly constant.
VEGA Pressure Transmitters
The VEGABAR 80 series use different types of diaphragms for different applications. Traditionally, most pressure sensors use an oil filled metallic diaphragm that separates the measuring cell from the process fluid. The VEGABAR 80 series differentiates itself from the competition by including ceramic measuring cells, too. These measuring cells are abrasion-resistant and provides a diaphragm 10 times harder than stainless steel.
Advantages
- Various configuration options for simple adaptation
- Multiple mounting configurations including “top down”
- Reliable measurement with temperatures up to 400˚C
- Low maintenance with wear-free ceramic measuring cell
- Accurate measurement to the last drop through the smallest measuring ranges
Related products
Related applications
Distillation column
Level and pressure measurement in the distillation unit
The heavy, highly viscous process material and extreme temperature are located in the bottom part of the distillation. For level control of residual feeds, a non-contact measurement is essential for reliability. Monitoring head space pressure at the upper end of refinery columns is important to ensure that the process is operating under ideal conditions.
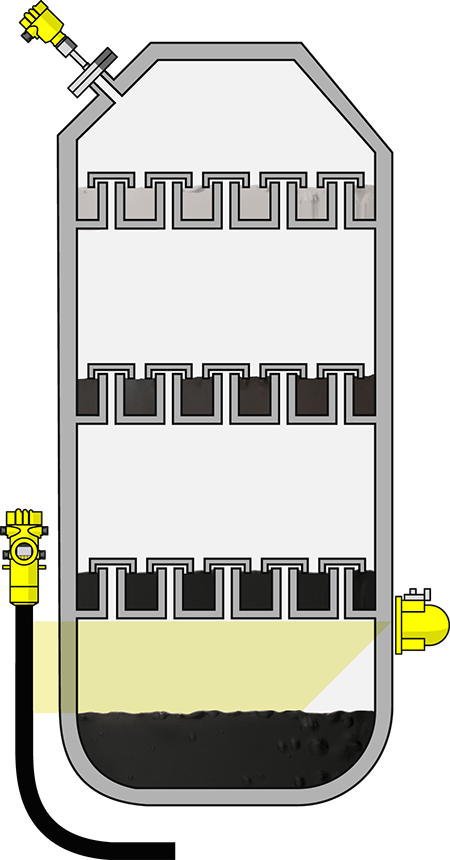
Reliable
Precise measurement results even in extreme environments
Cost effective
Easy mounting reduces installation and maintenance costs
User friendly
Simple calibration even during running process
Ice cream "Premix" mixer
Level and pressure measurement during the mixing of ice cream ingredients
The ingredients for making ice cream are accurately weighed and fed into a mixing tank, where the "premix" is made. Afterwards, the premix is passed through the homogenizer at a pressure of about 140 bar and then pasteurized at 80 °C. The level in the premix vessel and the pressure in the pipeline leading to the homogenizer need to be continuously monitored to ensure continuous ice cream production.
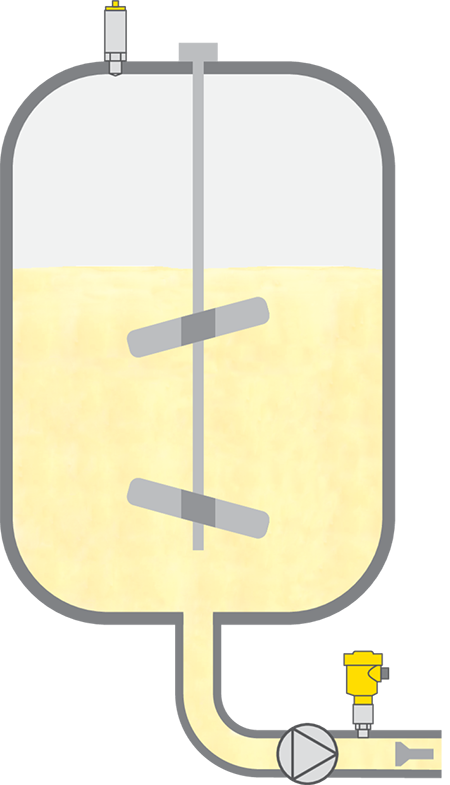
Reliable
Certified materials according to FDA and EC 1935/2004 regulations
Cost effective
Short delivery time and standardized operation thanks to plics® concept
User friendly
Simple installation due to small dimensions
Oil separators
Level and pressure measurement in an oil separator
The separator vessel contains a mixture of crude oil, gas, water and sand extracted from the subsea well. Precise monitoring of these multiple separation interfaces and emulsions play a vital role in ensuring the quality of the oil separator for separation. Exact control of interfaces, level and pressure allows optimum utilization of the oil separator and increases the effectiveness of the entire asset.
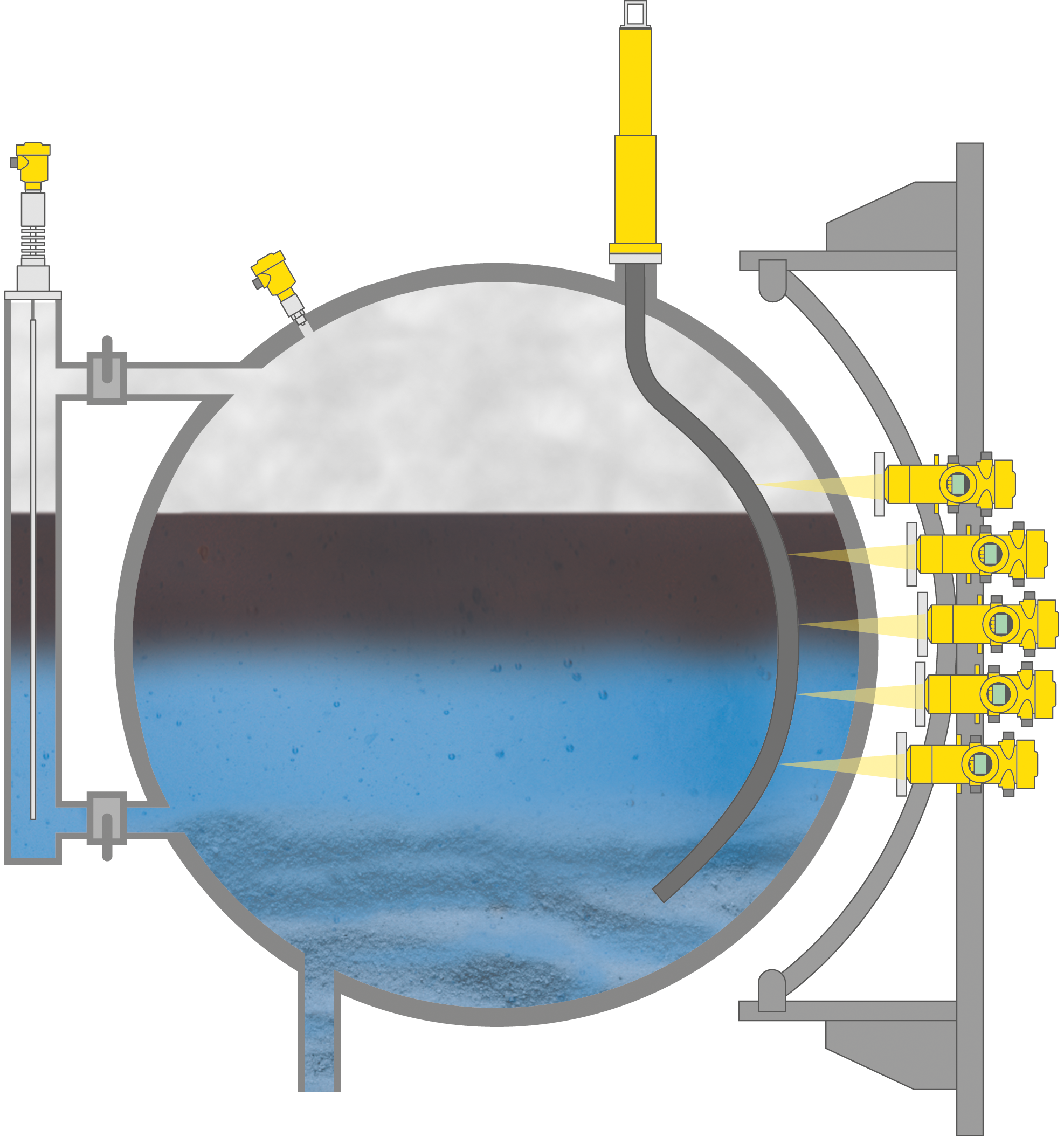
Reliable
Measurement results are unaffected by process conditions
Cost effective
Efficient operation and high oil quality
User friendly
Maintenance-free operation
Vibration and Capacitance: Liquid Level Switching
How it works
Liquid level switches detect when a certain predefined level is reached by the liquid inside a tank or vessel. These sensors are used when it’s not necessary to measure every possible level, like with continuous level measurement. A switch output can start and stop pumps, sound an alarm, or simply turn on a light. Point level switches can be integrated into a process control system.
VEGA Switches
VEGA uses four different technologies for liquid level switching: vibration, capacitance, microwave barrier, and radiometric.
Vibration switches, part of the VEGASWING series, are contact instruments that monitor frequency. These switches constantly vibrate at a specific frequency. The frequency changes once the liquid or fluid reaches the vibration switch, and this change activates the output.
Capacitance switches, the VEGACAP series, are also contact instruments, but these measure capacitance, or the liquid or fluid’s ability to hold an electrical charge. Once the liquid reaches the switch, the capacitance changes, and the switch output changes state.
Microwave barrier switches use two parts: a transmitter and a receiver. In between is an “invisible” barrier, and the switch is activated once that microwave barrier is broken or interrupted. These switches, called the VEGAMIP at VEGA, can provide “full” or “empty” options, and they can be used to determine when a liquid or fluid is pouring into a vessel. These can also be used as non-contact instruments by shooting through non-conductive vessels.
Lastly, radiometric switches operate similarly in principle to microwave barrier switches, but these instruments use gamma radiation emitted from a source holder while a detector measures the amount of radiation reaching it. Unlike any of the previously mentioned switches, radiometric switches can be installed completely externally, which is why they’re typically used to measure harsh or volatile processes like those seen in oil refining, the chemical industry, and mining.
Advantages
- Point level detection with low maintenance costs
- Vibration switches are simple plug and play instruments
- Capacitance switches work well with continual buildup
- Microwave barrier switches offer simple adjustment
- Radiometric switching is completely non-contact
Related products
Related applications
Steam drum
Level measurement and limiting device in the steam drum
High pressure steam is critical for the operation of the refinery. For the production and reliable supply of steam, accurate level measurement is required that allows efficient operation of the steam boiler. In addition to level measurement, high and low water limit detectors are also extremely important. As safety devices, they ensure that the water level neither exceeds the upper limit nor falls below the lower limit.
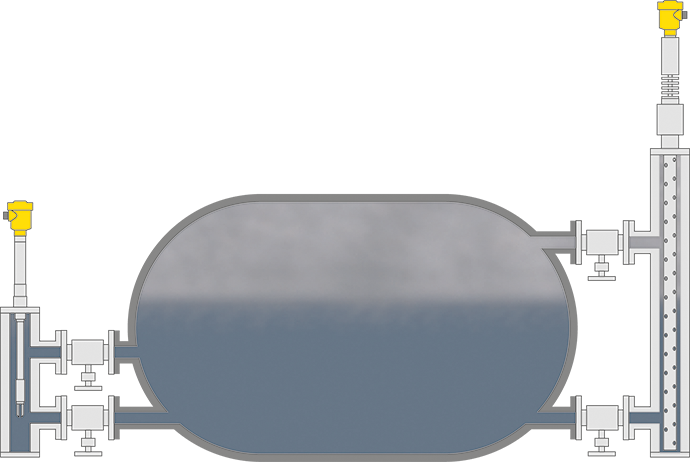
Reliable
High measuring accuracy independent of temperature and pressure
Cost effective
Low maintenance costs
User friendly
Simple installation
Conveyor belt
Mass flow measurement on conveyor belts
Bulk aggregates are fed into production processes via conveyor belts or screw conveyors. For effective feed control to and from these processes, or inter-production unit billing, the mass flow of the conveyed bulk material must be measured. A reliable belt-weighing scale system and mass flow rate ensures accurate measurement and smooth operation of the plant.
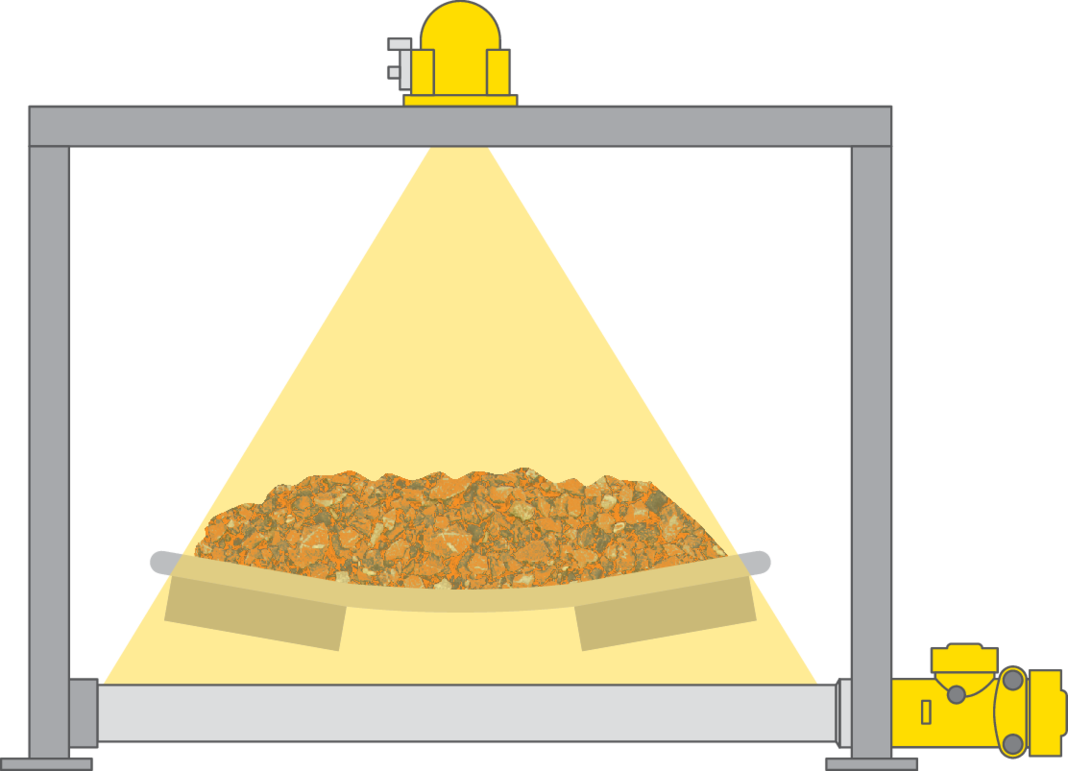
Reliable
Reliable measurement despite changing belt tension and vibrations
Cost effective
Optimal mass flow measurement allows exact accounting of bulk solids
User friendly
Maintenance-free operation
Pulper
Level measurement and blockage detection in the pulper and conveyor belt monitoring
Waste paper or pulp bales are transported on a conveyor belt to the pulper, where they are broken down by adding process water. A stirrer speeds up to separate fibers. Difficult process conditions exist in the pulper: falling bales cause severe pressure shocks, the stirrer creates vortexes. Besides that, foreign substances like wire, glass or sand enter the process along with the waste paper and have an extremely abrasive effect on the interior of the vessel. To ensure an automatic process flow, the level measuring system must establish the ratio of waste paper/pulp to process water. In addition, a possible jamming of the bales on the conveyor belt must be detected.
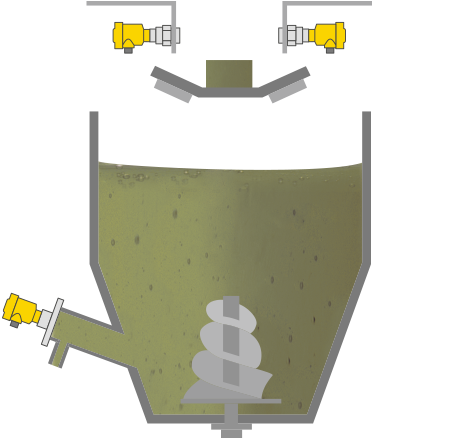
Reliable
Prevents jamming, thus ensuring a smooth automated process
Cost effective
Enables optimal ratio of pulp/waste paper to process water
User friendly
Wear and maintenance-free thanks to non-contact measurement
How it works
Radiometric level measurement sounds complicated, but the principle behind it is relatively easy to understand. Gamma radiation emits from a source holder, and a detector measures the radiation that reaches it. The amount of energy reaching the detector will vary based on the amount of liquid inside the tank or vessel. The electronics inside the detector use the gamma reading to infer a measurement and outputs the value.
VEGA Radiometric Sensors
The ProTrac Series is used for continuous level and point level monitoring in the most difficult liquid applications because they measure without contacting the process material. This means there is no chance of damaging the detectors with harsh, abrasive, or corrosive products that would require frequent and expensive maintenance. Plus, these instruments are impervious to thermal shock, drastic pressure shifts, and other extreme process conditions.
Advantages
- Maximum operational reliability even in the harshest environments
- Measurement is independent of pressure, temperature, and product aggressiveness
- Measuring system can be installed on the outside of a vessel during ongoing production
- Extending existing source life by retrofitting to ProTrac is made easy due to available adapter brackets
Discover the right radiometric instrument for your application
Related products
Related applications
Fluid catalytic cracking unit
Density, level measurement and point level detection in the reactor
Fluid Catalytic Cracking (FCC) is one of the most important conversion processes used in petroleum refineries. As with many other refining applications, the vessels in the reactor system need to be operated and controlled at their optimum levels, as this is critical for the process productivity. Maintaining the proper levels also ensures that the expensive catalyst is used at maximum efficiency, with no waste.
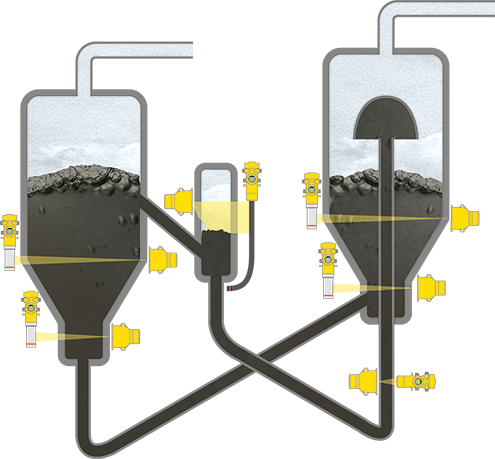
Reliable
Non-invasive measurement ensures highest plant availability
Cost effective
Lightweight design reduces mounting costs
User friendly
External mounting does not interrupt the process
Reboiler
Level measurement in the reboiler
Evaporators are heat exchangers that are deployed at the bottom of distillation columns. In the evaporator, the residue is boiled up from the sump and fed back into the distillation process. Precise control of the level in the evaporator ensures efficient operation of the plant. A reliable measurement also ensures that the heating coils are always covered with liquid, to prevent any overheating incidents.
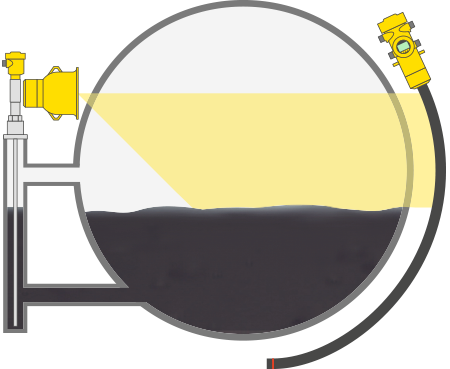
Reliable
Safe and reliable measurement even at extreme temperatures
Cost effective
Maintenance-free operation
User friendly
Easy installation
Cyclone
Buildup measurement in cyclones
In clinker production, cyclones are used to preheat the raw meal. Before the raw meal enters the rotary kiln it is preheated to +900 °C in the cyclone. Constant monitoring of the buildup thickness on the walls ensures a continuous process.
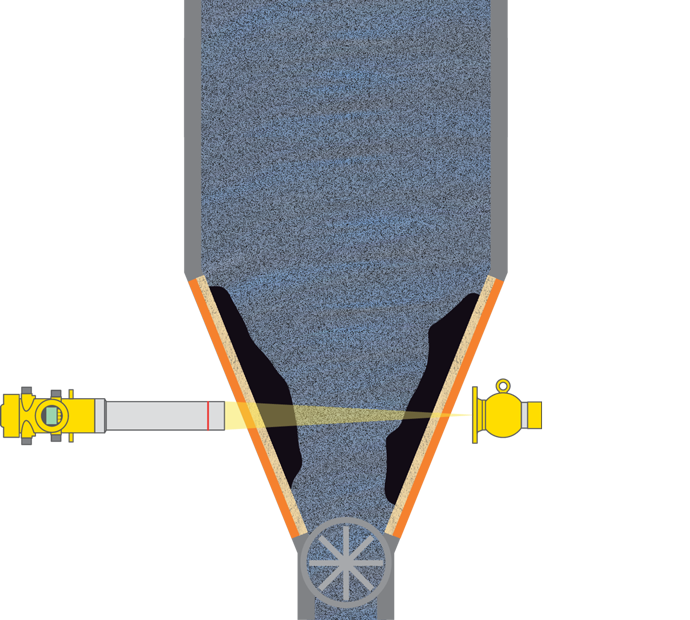
Reliable
Reliable buildup measurement despite high temperatures
Cost effective
Monitoring the formation of buildup ensures high availability of the cyclone
User friendly
Simple external mounting
How it works
Ultrasonic sensors emit ultrasonic pulses toward the liquid being measured from above. The surface of the liquid below reflects the signals back in the direction of the antenna system. The elapsed time from emission to reception of the signals is proportional to the level of the tank. The instrument uses this time of flight to determine a distance to the product surface, and then calculates a level inside using the known height of the tank or vessel.
VEGA Ultrasonic Sensors
VEGA’s ultrasonic sensors are ideal for simple, standard continuous level applications. The VEGASON sensors are a cost-effective, non-contact solution requiring little to no maintenance. These sensors are compact, allowing for easy installation, and they measure any liquid, independent of the its characteristics.
Advantages
- Non-contact liquid level measurement with high accuracy
- Cost-effective solution for simple applications
- Reliable measurement independent of liquid features
- Maintenance-free operation through non-contact measuring principle
Related products
Related applications
Conditioning
Level measurement in the conditioning tank
The applied chemicals and precipitants are suitably conditioned to ensure that they reach the wastewater in an optimal, low concentration. They are metered out according to the degree of pollution and mixed with the wastewater. Continuous level measurement is employed to ensure optimal metering control.
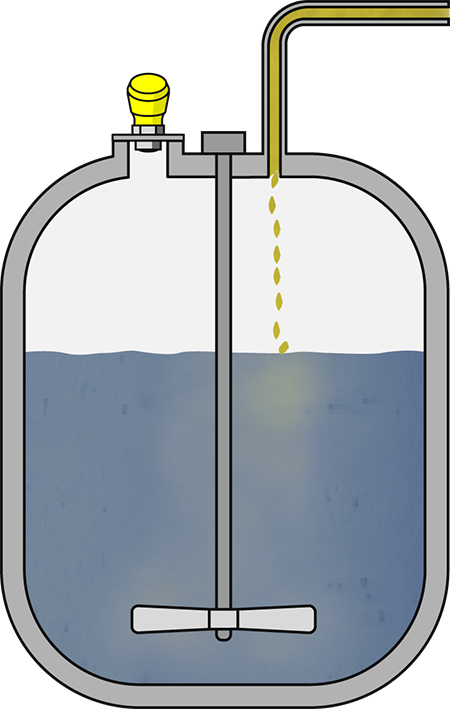
Reliable
High chemical resistance
Cost effective
Reliable measurement, independent of the medium properties
User friendly
Simple installation and setup
Storage tank for wet strength agent
Level measurement and point level detection in the storage tank for wet strength agent
Wet strength agents are polymeric additives that increase the water resistance particularly of hygienic and specialty papers. These are applied in the paper machine via a size press or spraying device. Because of their high pH value, these substances are stored in double-walled GRP (glass reinforced plastic) tanks. For safety and operational reasons, multiple level measurements are needed in these tanks.
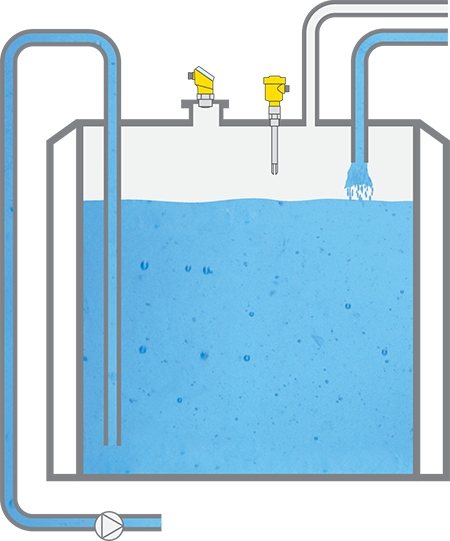
Reliable
Reliable filling with overfill protection and leak sensors
Cost effective
Maximum utilization of the container volume thanks to continuous level measurement
User friendly
Direct reading of the measured value at the additive station
Conveyor belt for sugar beet
Measuring the level of sugar beets on the conveyor belt
The delivered sugar beets are poured from trucks onto conveyor belts that transfer it to the washing and shredding facility. Multiple level sensors are required to monitor the loading of the beet as it goes on the conveyor belt to optimise the feed rate and energy usage.
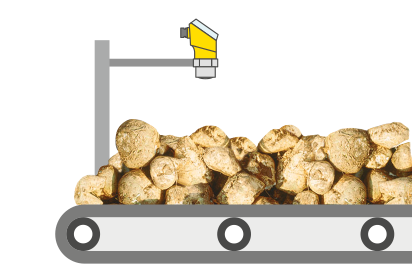
Reliable
Reliable monitoring of belt loading
Cost effective
Measurement enables optimal control of the flow rate
User friendly
Simple setup and maintenance-free operation
Export this article
Download as PDFShare this article
Comments ({{comments.length}})
{{getCommentAuthor(comment, "Anonymous")}} {{comment.timestamp | date : "dd.MM.yyyy HH:mm" }}
{{comment.comment}}