Monitoring flour production more reliably with VEGAPULS 80-GHz radar sensors
Harinas Elizondo supplies more than 7,000 baked goods manufacturers, from small bakeries to large industrial customers, with customised wheat products. Its product range includes special flour varieties for tortillas, pizzas and baguettes as well as puff pastry, biscuit and cakes. Product names like “Maite”, “Osasuna” or “Hoja de Plata” are well-known on the market as coarse, dark or white, or extremely fine grades.
Good visibility despite dust and internal fixtures
But inside tall, slender silos, the necessary installations and struts can cause problems for non-contact sensors during measurement. This is where the special feature of VEGAPULS 69 sensors makes the difference: its precision focusing helps separate the measuring signal from interference signals. With an aperture angle of only 3.5 degrees, the measuring beam flies right past obstacles.
Thanks to the reliable measurement data, the technicians and milling specialists in the three production facilities of Harinas Elizondo understand much better what’s going on inside the various processes. This helps them improve process reliability, increase plant availability and ensure reproducible product quality.
High quality at every step: from raw material to finished product
Customers rely on it
When measuring inside the tall, slender silos, anything that gets in the way, like internal fixtures and struts, are a big challenge. The precise focussing of VEGAPULS 69 sensors helps separate the measuring signal from interference signals.
With the same thoroughness it applies in monitoring product quality, the mill subjected the VEGA sensors to a tough practical test before deciding to implement them in production. “We wanted to be absolutely sure that the sensors could live up to our high standards,” recalls Victor Menchaca Ortiz. And that was because the company had previously tried sensors, including guided radars, from other manufacturers and had been disappointed, as they were simply not as reliable as expected. Today, the project planner is convinced that he has found the right solution. He’s quite enthusiastic about the accuracy of his numerous measuring points. The simplicity of integration also exceeded his expectations: “Everything on the sensors can be easily replaced if it should ever be necessary. After installation, I was able to set the parameters handily via Bluetooth. This saved me having to climb up to the top of the silo again.”
Orders of all sizes
Instrumentation with VEGA measuring instruments fits in with this concept perfectly. Using VEGASCAN 693 controllers, the Polanco plant communicates its process measurement data via Ethernet to the decentralised control system, and thus controls all incoming and outgoing stocks at all times. In addition, the Bluetooth configuration enables remote visualisation and management of all measuring points via mobile phone or tablet.
Despite all the automation, engineer Menchaca Ortiz is of the opinion that “the human factor” must definitely not be overlooked. He’s convinced that the skills and experience of the employees are still the most important resource at Harinas Elizondo. He also values personal consulting and support highly. Besides perfect measurement technology, an honourable service philosophy is what makes the difference for him. “VEGA’s technical support is not only fast and extremely efficient, it’s performed with just as much passion as we have for our work.”
Related industries
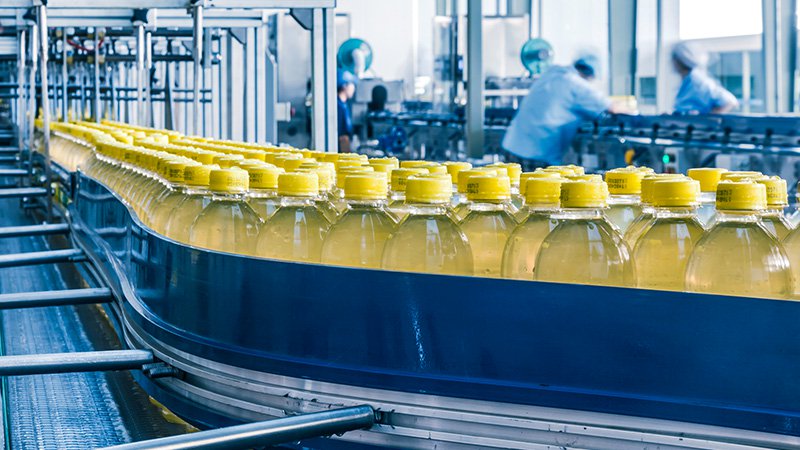
Food industry
Anwendungen
Flour silo
Level measurement in the flour silo
The different varieties of flour are most often stored in tall silos with very narrow chambers. Filling takes place regularly and is done pneumatically from the top. In order to produce the desired blend of different varieties at any time, a reliable level measurement in the individual silos is essential, even during filling. The process challenges include dust generation, strong air movement and a poorly reflecting product surface.
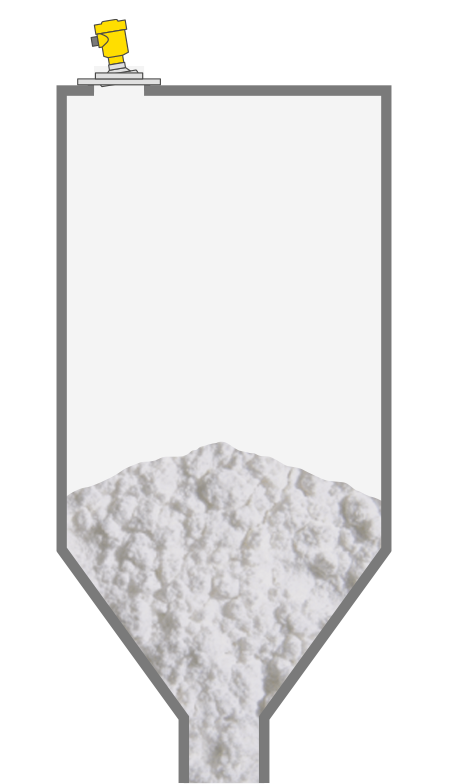
Reliable
Non-contact measurement, no wear and tear
Cost effective
One sensor for all silo heights
User friendly
Integrated cleaning system
Grain silo
Level measurement and point level detection in the grain silo
Barley is stored in malt houses in silos up to 20 metres high before it is processed into malt for production of beer. Filling the silos generates a lot of dust and the material cone geometry constantly changes during the filling and emptying process. A reliable indication of the level ensures the smooth operation by sending signals corresponding to the level or possible limit levels of the grain.
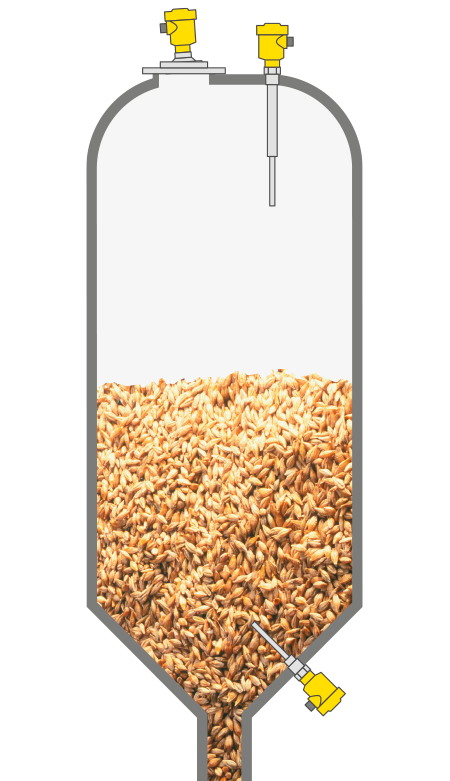
Reliable
Reliable measurement independent of the medium
Cost effective
Better utilisation of silo capacity and product through reliable measurement
User friendly
Simple calibration
Export this article
Download as PDFShare this article
Comments ({{comments.length}})
{{getCommentAuthor(comment, "Anonymous")}} {{comment.timestamp | date : "dd.MM.yyyy HH:mm" }}
{{comment.comment}}