Radar technology can now be used even in small containers
The big advantage of radar technology is its ability to measure under different and changing process conditions across a variety of media. However, up until now, the use of the sensors in small vessels was very limited, because sensors were not available with the necessary small process fittings as well as not achieving the accuracy and measurement certainty required at very close range.
Guided radar has been used as an interesting alternative, but it quickly reaches its limits in applications with very strong product movement, agitators and the very high demands on hygiene.
Although the close range of radar sensors is not limited by a dead band, the previous technologies were often subject to limitations because the interfering signals from the antenna system could cause accuracy problems or even obscure the echoes from the product surface.
The solution
The high frequency of VEGAPULS 64 not only facilitates the use of significantly smaller process fittings, it also ensures significantly better measurement performance when the sensor is used in small vessels. The large sensor bandwidth produces very narrow echo signals, which enables a significant increase in measurement accuracy, even at close range.
The use of new antenna technologies for 80 GHz frequency range has assisted in reducing the interfering signals at close range – the result is significantly higher measurement reliability right in front of the antenna. Due to these significant performance enhancements, VEGAPULS 64 can also be used in smaller vessels.
The benefits
- Accurate, universal radar technology can be used in very small vessels
- Non-contact, hygienic and wear-free measurement
- Easy replacement of existing technology thanks to the process fittings
Expert tip:
The strength of the reflected signal is determined by the medium and the size of the antenna. Level measurement directly in front of the antenna is more challenging when the medium reflects poorly and the antenna is very small. When measuring oil products with a ¾" antenna system, it is a good idea to maintain a minimum distance of 10 - 15 cm which can be achieved with a stand-off nozzle, but if larger process fittings are used, this distance can be considerably shorter.
Applications
IBC-Tank (metallic)
Level measurement of liquids in transport containers
In many of the production processes in the chemical industry, small quantities of various chemicals are needed in order to improve the characteristics of certain products. The media are often provided directly to the production areas in small, transport containers. Accurate level measurement ensures a continuous supply of materials for production.
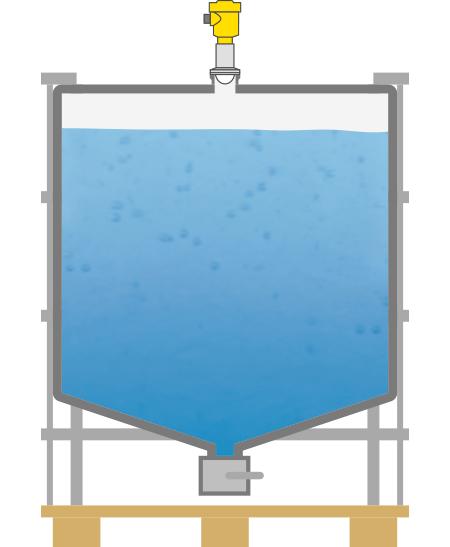
Reliable
Accurate measurement down to the bottom of the vessel
Cost effective
Sensor is quick and easy to install
User friendly
Visualised display of measurements
Batch filler vessel
Level measurement in the batch filler vessel
The small batch filler vessels around 1 m high and 60 cm diameter alongside the production facility supply the filler heads of the tank. The products vary from conserve to peanut butter to chocolate spread, with varying viscosity and temperatures. The product density is also changing from each batch. The level system is required to enable an optimal filling of jars.
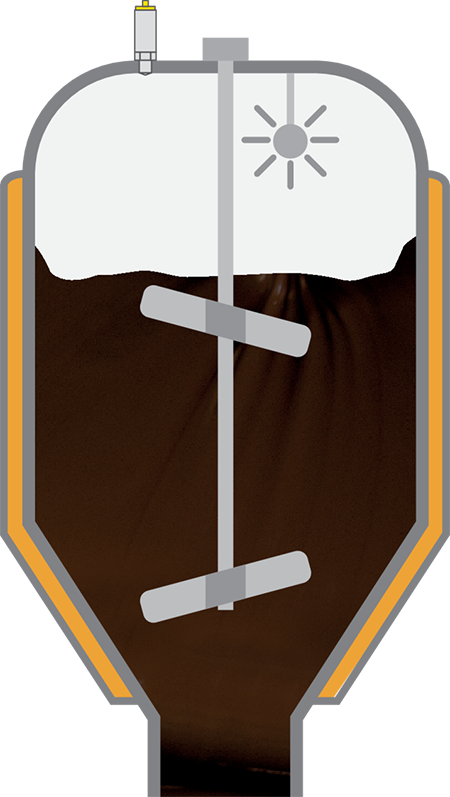
Reliable
Measurement independent of density and viscosity
Cost effective
Accurate level measurement optimises use of jars and medium
User friendly
Simple setup
CIP system - cleaning agent storage tanks
Level measurement and point level detection in the cleaning agent storage tank of the CIP system
In the pharmaceutical industry, cleaning of process equipment takes place within the framework of a validated "Clean in Place (CIP)" process to ensure aseptic conditions are maintained in production equipment, tanks and pipelines. Sodium hydroxide or concentrated acids are frequently used as cleaning agents, which are held in storage tanks within the CIP system. They are diluted in a premix vessel prior to use. Level measurement enables safe storage and optimal usage of these cleaning agents. Point level detection serves as overfill and dry run protection.
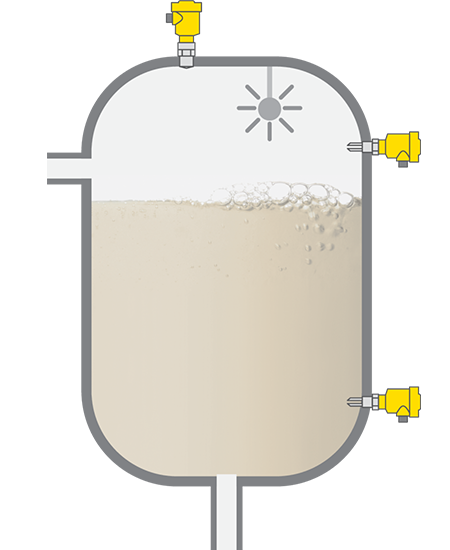
Reliable
Approved materials in compliance with FDA and EC 1935/2004
Cost effective
Maintenance-free operation
User friendly
Simple mounting
Small containers
We need your consent
This content is provided by an external provider. If you activate the content, personal data may be processed and cookies set.
Export this article
Download as PDFShare this article
Comments ({{comments.length}})
{{getCommentAuthor(comment, "Anonymous")}} {{comment.timestamp | date : "dd.MM.yyyy HH:mm" }}
{{comment.comment}}