Ceramic measuring cells – corrosion-resistant, robust, precise
One of the most important parameters to be monitored in chemical industry processes is pressure. That’s because pressure and differential pressure values can be used to determine things like; levels, volume, flow or filter performance, among many others. However, especially in the chemical industry, pressure sensors also have to meet special requirements,. VEGA instruments are built to meet these requirements – with metallic and more importantly ceramic measuring cells.
Metallic measuring cell: Reliable solution
Metallic-based pressure sensors, just like the VEGABAR 83, have been ensuring safety and reliability in chemical plants for decades. They are usually made of high-quality stainless steel such as 316L or other specialist alloys. This makes them ideal for use under harsh conditions. With the correct materials in there design, they can withstand high-pressure applications and extreme temperatures.
Ceramic measuring cell: an optimal alternative
In-house development and production
VEGA is one of the few manufacturers in the world that develop and produce their own ceramic measuring cells like CERTEC®. It is the key element of a ceramic pressure sensor. In an extremely complex manufacturing process, the diaphragm and the base body of aluminium oxide ceramic are printed with gold paste under clean-room conditions and joined together with glass solder at high temperature to form the measuring cell.
The many advantages of ceramic
Besides high corrosion resistance, the ceramic measuring cell also offers the following advantages:
- First-class long-term stability
- High reliability
- Outstanding overload resistance
It enables precise measurement over a long period of time. The ceramic measuring cell is often met with initial skepticism, as the material is assumed to be susceptible to breakage. “This is an unjustified concern,” explains Robin Müller, product manager at VEGA. “Ceramic measuring cells have a significantly higher overload resistance than metallic cells. Metallic diaphragms can deform irreversibly when exposed to very high pressures or shocks, a ceramic diaphragm simply deflects until it touches the base body and then returns to its original position.”
Dry and robust
Another argument in favour of the ceramic measuring cell: it is a dry cell, i.e. free of oil. In the event of a diaphragm rupture, no substance can escape to contaminate – unlike with a metallic measuring cell, where oil often needs to be used as the transmission medium.
Planners and operators also take advantage of this when it comes to measuring aggressive and toxic gases, as safety plays a particularly important role in such cases. But even in applications with the VEGABAR 82 and 83 in acids and alkalis, VEGA can offer highly resistant materials for process fittings and measuring cell – and with a “Second line of Defense” as well. This means the measuring cell is separated from the electronics by a gas-tight, glass feed-through.
Temperature shocks? No problem!
The sensitivity of ceramic sensors to moisture and temperature shocks – once a great disadvantage compared to metallic measuring cells – is no longer a problem. For one thing, the process temperature is measured, and the value is calculated to compensate for the influence of temperature on the measured pressure value. At the same time, a second temperature sensor in the glass seam behind the ceramic diaphragm detects even the smallest temperature changes. An algorithm built into the sensor electronics ensures that temperature shocks are compensated for. “This quite sensitive temperature measurement value can be utilised for process temperature monitoring and also transmitted as a separate signal,” says Robin Müller, describing another useful function.
Suitable for hydrogen
Applications involving vacuum or hydrogen present special challenges for measurement technology. The boiling point of liquids drops in a vacuum. As a result, the oil in the metallic measuring system may begin to boil at temperatures below the atmospheric boiling point, causing significant errors. Also, hydrogen presents another, but no less significant, hurdle: Hydrogen molecules can penetrate metal – even the thin diaphragm of a metallic pressure measuring cell. “If hydrogen diffuses into and through the diaphragm, it contaminates the transmission oil behind it,” explains Robin Müller. The resulting hydrogen deposits can lead to a permanent change in measurement performance.
Besides diffusion, a metallic diaphragm material can also become brittle with hydrogen. But it is not an issue if diffusion-tight fittings and resistant materials, such as gold/gold-rhodium coatings are used, as VEGA provides with sensors in hydrogen applications. The dry ceramic measuring cells play an important role here: “Even if hydrogen were to get into the measuring cell, it will not cause any damage,” says Robin Müller. “Ceramic pressure sensors are a good solution for use in hydrogen production via electrolysis, which works at low pressures.”
Differential pressure measurement made easy
In chemical applications, differential pressure measurement delivers important data on flow, level and tank pressure. It can be used, for example, to
- measure the level in a pressurised vessel
- determine the flow rate at orifice plates and other flow elements
- monitor a filter or heat exchanger
Differential pressure measurement without using impulse lines: Two electronically connected sensors make it possible.
In this episode of VEGA Talk, Stefan and Tom show what makes the ceramic measuring cell from VEGA so stable:
We need your consentThis content is provided by an external provider. If you activate the content, personal data may be processed and cookies set.Related industries
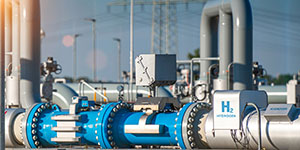
Hydrogen
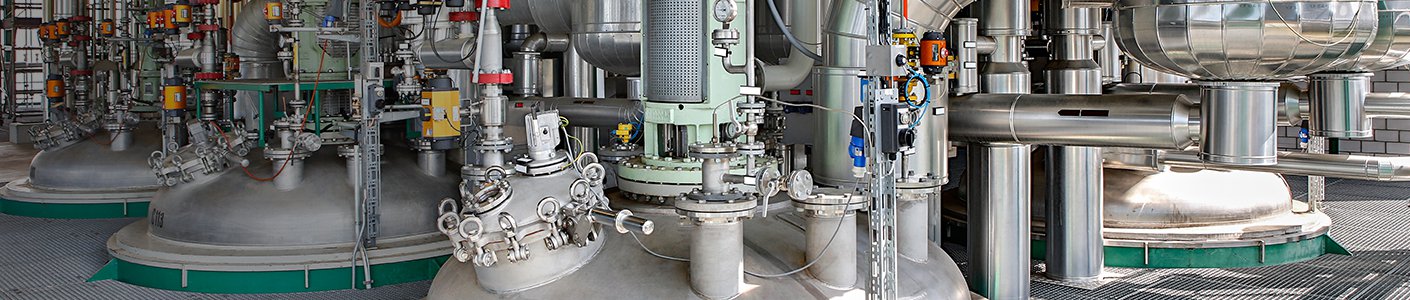
Applications
Products
Export this article
Download as PDFShare this article
Comments ({{comments.length}})
{{getCommentAuthor(comment, "Anonymous")}} {{comment.timestamp | date : "dd.MM.yyyy HH:mm" }}
{{comment.comment}}