Small but robust: The RFID tag contains all important sensor information and the identification data remains permanently accessible, even in harsh environments.
Readable under difficult conditions
VEGA sensors are heading into the future with RFID tags
Scratches, dents or worn areas: After years of reliable performance under diverse environmental conditions and temperatures, even a level sensor shows its age. To make it possible to identify a sensor at any time and in any place, even if its type label is damaged or faded, and trace it using every digit of the serial number, VEGA is making RFID tags available for its sensors, initially for those of the PRO series.
RFID (Radio Frequency Identification) is not new, but it is now probably the most advanced way of identifying sensors in industrial facilities.
RFID tags contain a microchip that stores information. Because their robust chips make them contactlessly readable for many years, despite wind and weather, rapid temperature changes or exposure to sunlight, they are far superior to other labelling techniques. “They are an ideal addition to stamped tags or barcodes, especially for outdoor installations,” says Stefan Kaspar, VEGA product manager. Whether in a sprawling chemical park or in a tank farm in the oil and gas industry: “With an RFID tag, our sensors can be reliably tracked even after years of intensive use in the field.”
Universal standard
Sensor labelling is not only based on direct customer requirements, but also on the internationally valid IEC 61406 standard and the DDCC, a cross-manufacturer association of plant operators, service providers and manufacturers of machines and components for process automation that has been in existence for three years now. Kaspar explains: “As a member of the Digital Data Chain Consortium, we are working together with many companies on an industry-wide standard for data exchange.” The consortium has a clear vision: “In the future, access to and exchange of information between all involved parties should be made easier over the entire life cycle of a device or component.” No matter who the manufacturer is. By simply scanning the QR code on the type label with a normal photo app – or by reading out the RFID tag – users will in future be able to uniquely identify their assets and access the associated documentation.
Digital Twin
The big breakthrough is still a long way off, but the future has come a giant step closer with the current ID solution. “No matter where you are in a plant: In the future, you’ll be able to access a unique sensor identity anywhere with just one click,” says Kaspar, “and go from there directly to the digital twin, which contains all the important information about the device over its entire life cycle, from documentation to parameterisation to proof tests carried out, as well as information for repair and recycling.” The RFID tag for VEGA sensors is thus the first step on the way to the digital twin.
Measuring point identification
Alternatively, the RFID tag can also be labelled with a unique measuring point ID provided by the customer. This specific, unambiguous labelling helps to avoid adjustment errors and provides orientation. Kaspar is convinced: “From maintenance to inspection to servicing, this makes plant operation more efficient and safe.” The RFID tags are initially available for the VEGAPULS 6X radar level sensor and will be introduced for all other PRO instruments later.
Info:
The company
VEGA Grieshaber KG has been developing innovative level and pressure measurement technology since 1959. As the world market leader in radar, the company is driving forward new technologies, doing research and developing state-of-the-art sensors for many different sectors, such as drinking water supply, energy generation and the pharmaceutical industry. VEGA employs more than 2,400 people worldwide – around 1,200 of them at company headquarters in Schiltach. Together with its subsidiaries and sales partners, VEGA is active on the market in more than 80 countries.
Personal contacts
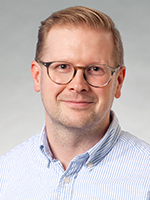
Christoph Wöhrle
Press Officer, Corporate PR
Close