Why is the dynamic range of a radar device important?
The dynamic range of a radar sensor defines which applications the sensor can be successfully used in. The reflective properties of various bulk solids dier
greatly. A large dynamic range ensures that even the smallest signals and therefore the widest range of products can be measured.
The theory
The dynamic range of a sensor indicates the dierence between the largest and smallest signal that can be measured. Since the transmitting power cannot be increased, the electronics has to detect and evaluate ever smaller signals.
The solution
VEGAPULS 69 sets new standards. Because of its large dynamic range, it can measure even the tiniest of reflected signals. This ensures even better measurement certainty and reliability for media with good reflective properties – such as coal, ore or rocks. When it comes to the measurement of media with poor reflective properties, such as plastic powders or dry wood chips, this new technology comes into its own, with significantly improved signal dierentiation.
The benefits
- Broader range of applications for all bulk solids, regardless of their reflective properties
- Universal measuring method thanks to the large dynamic range
Expert tip:
When selecting a sensor for bulk solids applications, it makes sense to opt for a sensor with the largest possible dynamic range. Such a sensor always ensures maximum reliability, regardless of the measuring range and the type of application.
Applications
Cement silo
Level and pressure measurement and point level detection in cement silos
Before further processing, the cement is stored in tall silos. The cement is transported both in and out of the silo via pneumatic conveying. Efficient storage and transport of the product is ensured by accurate level measurement and point level detection, as well as also monitoring the pneumatic conveying system pressure.
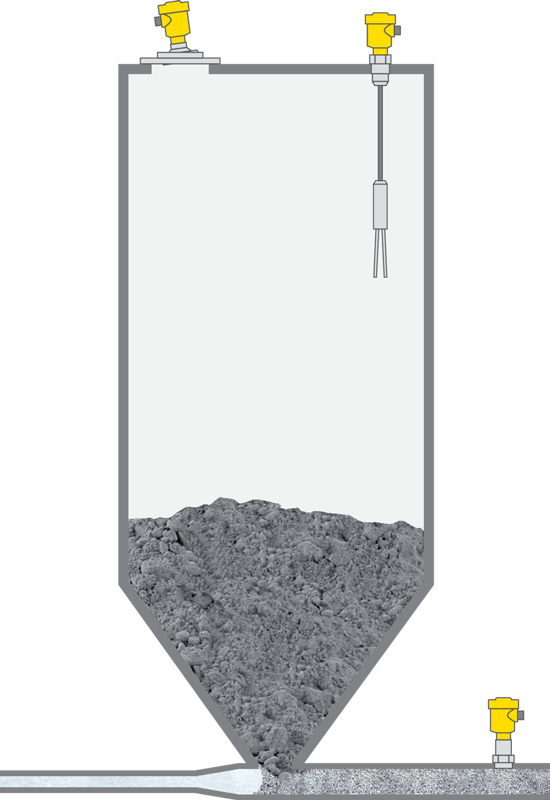
Reliable
Reliable measurement ensures a continuous supply of raw material
Cost effective
Optimal stocks enable continuous production
User friendly
Maintenance-free operation
Silos for bulk solids
Level measurement and point level detection in silos
In the chemical industry, many different kinds of bulk solids are produced or used as raw materials. To ensure reliable measurement of silo contents, many factors must be considered: different bulk densities, abrasive properties, dust generation and the requirements of explosion protection. Implementation of the most suitable level sensors ensures optimal production planning and reliable logistics for the finished products.
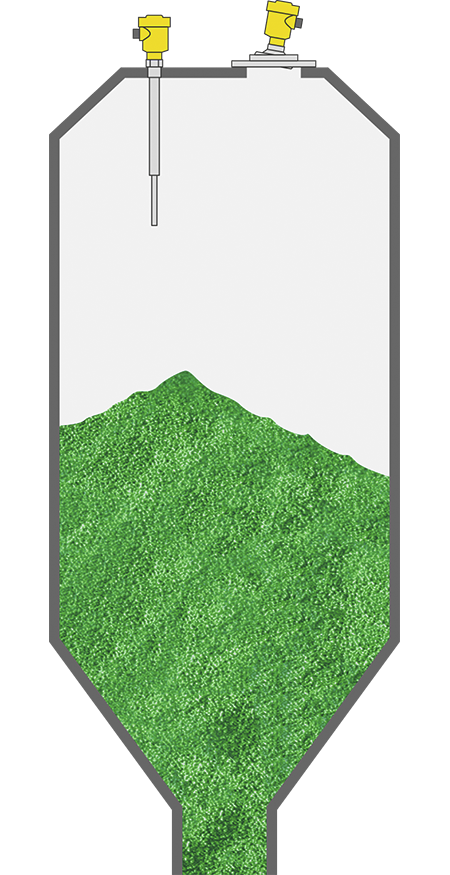
Reliable
Reliable measurement, independent of media properties and container geometry
Cost effective
Maintenance-free operation
User friendly
Universally applicable for almost all bulk solids
Grain silo
Level measurement and point level detection in the grain silo
Barley is stored in malt houses in silos up to 20 metres high before it is processed into malt for production of beer. Filling the silos generates a lot of dust and the material cone geometry constantly changes during the filling and emptying process. A reliable indication of the level ensures the smooth operation by sending signals corresponding to the level or possible limit levels of the grain.
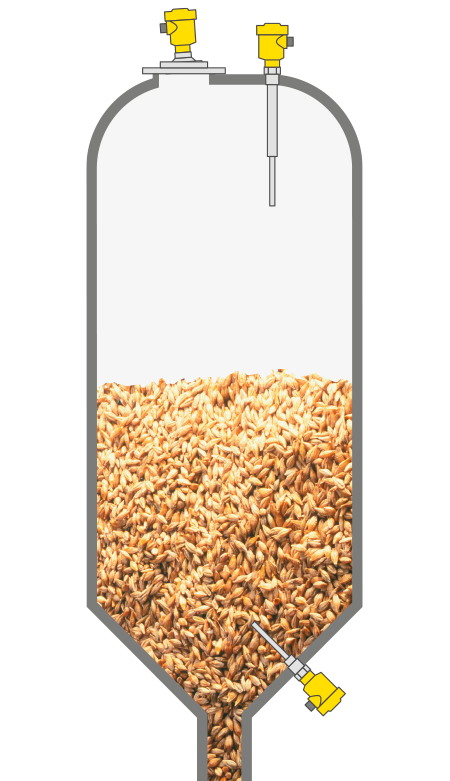
Reliable
Reliable measurement independent of the medium
Cost effective
Better utilisation of silo capacity and product through reliable measurement
User friendly
Simple calibration
Export this article
Download as PDFShare this article
Comments ({{comments.length}})
{{getCommentAuthor(comment, "Anonymous")}} {{comment.timestamp | date : "dd.MM.yyyy HH:mm" }}
{{comment.comment}}