Always reliable measurement, even with build up and deposits
In the past, contactless level sensors had to be cleaned at regular intervals or freed of deposits by means of a rinsing connection or removal for hand cleaning. With many conventional sensors, buildup or condensation on the process fitting reduces the reliability of the measuring results. Especially in small containers, performance compromises often had to be made.
The solution
The antenna system of VEGAPULS 64 is encapsulated in PTFE or PEEK, so there are no cavities or crevices in which product can accumulate. The surface of the material is very finely processed with diamond tools, which also considerably reduces product adhesion. In addition, special software algorithms filter out interference caused by buildup on the antenna system. Thanks to the high dynamic range of the sensor, signal attenuation caused by product deposits is largely compensated. This allows the level to be reliably detected even with contamination on the sensor.
- High measurement certainty, even with product deposits collecting during operation
- Measurement independent of condensation and system quickly available after cleaning cycles
- Non-contact measurement enables maintenance-free operation
Extreme product buildup due to condensation or crystallization on the sensor can be significantly reduced if the flange is provided with insulation. Thermal bridges are thus avoided and deposits kept to a minimum. VEGAPULS 64
Related applications
Thickener for sugar beet juice
Level measurement in a thickener
The thin juice extracted from sugar beet is thickened by the reduction of excess water in multiple stages at the evaporator station. This evaporation process is carried out under vacuum and heat. The liquid in the evaporator boils so violently that great amounts of vapour are formed. A level sensor is needed to monitor and control the thickening process.
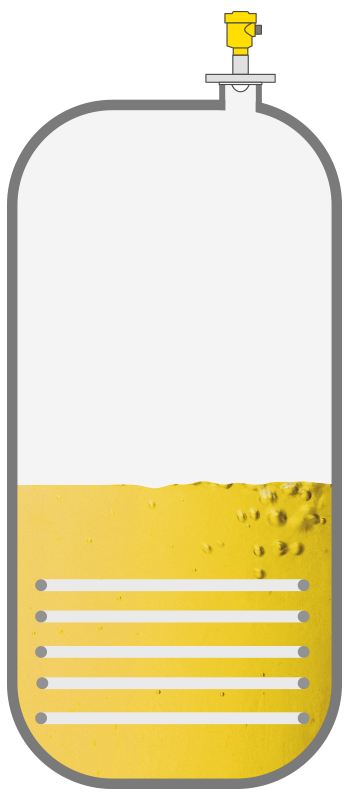
Reliable
Accurate, reliable measurement, even under adverse vacuum and condensation conditions
Cost effective
Reliable measured values allow efficient control of the evaporation process
User friendly
Narrow beam angle allows easier installation in vessel top
Ice cream "Premix" mixer
Level and pressure measurement during the mixing of ice cream ingredients
The ingredients for making ice cream are accurately weighed and fed into a mixing tank, where the "premix" is made. Afterwards, the premix is passed through the homogenizer at a pressure of about 140 bar and then pasteurized at 80 °C. The level in the premix vessel and the pressure in the pipeline leading to the homogenizer need to be continuously monitored to ensure continuous ice cream production.
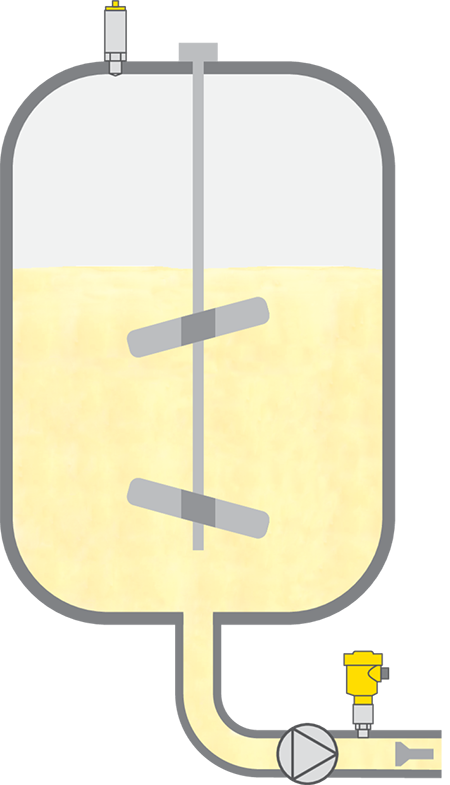
Reliable
Certified materials according to FDA and EC 1935/2004 regulations
Cost effective
Short delivery time and standardized operation thanks to plics® concept
User friendly
Simple installation due to small dimensions
Preparation tank for solvents
Level measurement in the preparation tank for solvents
The various solvents and intermediate carrier materials have to be first prepared before they proceed onto further production steps. This is usually carried out in bioreactors and fermentation tanks. These vessels are enclosed with a steam heating jacket to regulate the temperature inside the mixing process. The level measuring system is needed to control filling and discharge as well as monitor during the process. Level detection prevents the tank from overfilling or running empty.
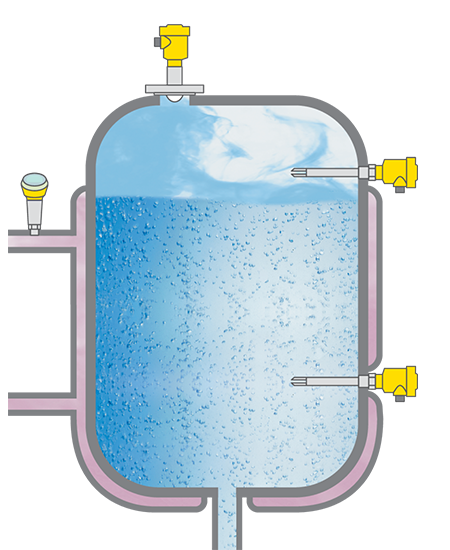
Reliable
Approved materials in compliance with FDA and EC 1935/2004
Cost effective
Maintenance-free operation
User friendly
Simple installation
Condensate and buildup
We need your consent
This content is provided by an external provider. If you activate the content, personal data may be processed and cookies set.
Export this article
Download as PDFShare this article
Comments ({{comments.length}})
{{getCommentAuthor(comment, "Anonymous")}} {{comment.timestamp | date : "dd.MM.yyyy HH:mm" }}
{{comment.comment}}