Vibrating level switch with turbo drive ensures reliable measuring signal
The vibrating level switch VEGASWING 66 works reliably and thus encounters the difficult ambient conditions in the thermal power plant.
Sometimes, seemingly difficult measurement situations can be solved by applying simple technologies – provided these are robust enough to withstand the challenging environments. This is what happened at the Jining Thermal power plant of China Huaneng Group Co, Ltd. in Jining, in the eastern Chinese province of Shandong. There, the vibrating level switch VEGASWING 66 simplified in one fell swoop the level measuring point that had previously been considered hopelessly complicated.
The production process in the Chinese thermal power plant in Shandong (capacity 380 MW) employs a high-pressure steam bypass system, which, to be sure, mainly takes effect only when the turbine is started up. When the turbine starts, water in the boiler is heated, generating steam. At this point, however, the steam parameters do not yet correspond to the operating state of the turbine. The temperature of the steam is still too low and it contains too much moisture. And it is exactly this that is problematic for the turbine, since very fine water droplets hit the turbine blades at high speed, possibly damaging the turbine blades. For that reason, the steam from the boiler is first passed through a bypass system. Only when the steam is in the right condition – i.e. without water droplets and at operating temperature – is the system switched off and the steam fed into the turbine.
When the steam bypass system is used, water collects at the bottom of the pipe. If the water is not drained in time, the pipe gets flooded, which can lead to problematic situations. So the water level must be accurately measured and lowered at the right time. In the past, the water in the turbine's steam bypass system was detected by a float switch. Due to frequent error signals, system shutdowns occurred again and again. To remedy this situation, the plant operator tried to find a level switch that would function reliably even at high temperatures (up to 325.5° C) and high pressures (38 bar).
Condensate storage tanks
Level measurement and point level detection in condensate storage tanks
Throughout the different process units, there are storage vessels that collect clean, reusable condensate. This condensate accumulates from the steam system that is used to heat the various hydrocarbon processes. The condensate tanks routinely have extremely high process temperatures, so a level measurement and point level detection are necessary that can withstand this environment.
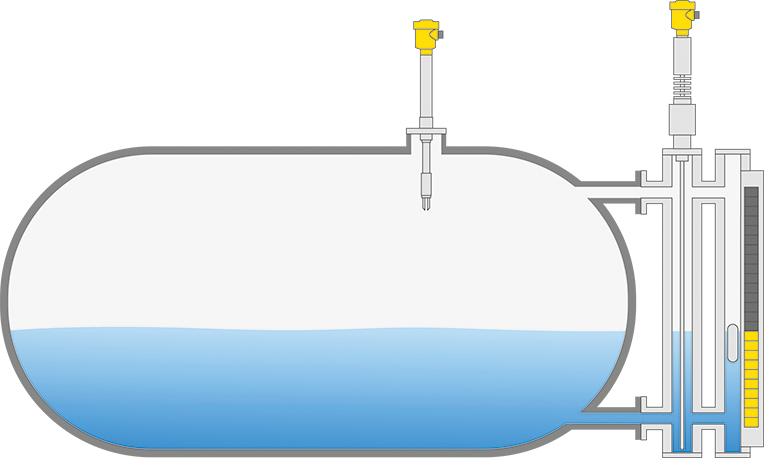
Reliable
Safe measurement unaffected by high temperature and steam
Cost effective
Maintenance-free through optimal redundancy arrangement
User friendly
Simple setup and installation
Steam pipe
Condensate detection in the water-steam cycle
To warm up the water for the boiler, steam is bled from the power plant turbine and delivered into a preheater. As the steam cools and condenses, it is removed from the preheater with pumps. Any condensate gathering in steam pipes has to be reliably detected to prevent it from entering the turbine. Vibrating level switches, mounted at low points in the system, reliably detect any water accumulation.

Reliable
Optimum protection of the turbine against condensation
Cost effective
Simple mounting and dependable function
User friendly
Function test via test button
Inductive drive as a solution for measurement under extreme temperatures
No one was able to come up with a convincing solution here until the advent of VEGASWING 66. This sensor’s core technology is a brand-new type of drive. Its patented inductive drive effortlessly manages to excite the tuning fork even under extreme temperature conditions. This means the user can take advantage of the simple installation and handling of a vibrating level switch, yet have an extended temperature range of -196° to +450° C and a pressure range of -1 to +160 bar. The sensor was thus the perfect choice for level detection in the steam bypass pipe.
Another advantage is that the sensor monitors itself and allows a function test to be initiated at any time to check if the sensor is in good working order. Corrosion on the fork, for example, would be reported immediately. The function test is carried out by simply pressing a button. In addition, the sensor is SIL2 qualified and can be used in homogeneously redundant systems up to SIL3.
We need your consentThis content is provided by an external provider. If you activate the content, personal data may be processed and cookies set.
Related products
Related industries
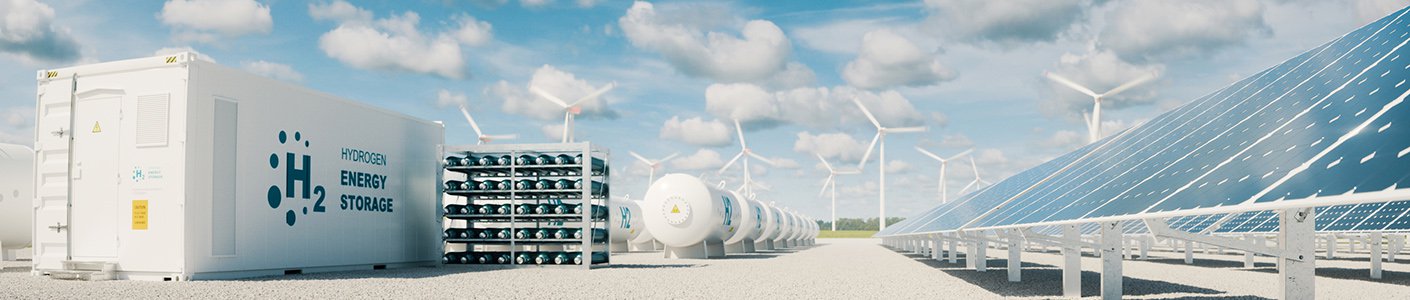
Energy
Export this article
Download as PDFShare this article
Comments ({{comments.length}})
{{getCommentAuthor(comment, "Anonymous")}} {{comment.timestamp | date : "dd.MM.yyyy HH:mm" }}
{{comment.comment}}