Solid Level Detection Sensors and Measurements
Knowing the amount of bulk solids inside a silo, tank, or other vessel is an important variable in any process to maximize efficiency, prevent overflows, running out, or for tracking volume or mass. A common way to monitor these variables is by measuring the level. This can be something as simple as a full or empty signal, or it can be a continuous level measurement to track and control the level changes during a process.
To measure level in a bulk solids container, there are a number of different technologies used ranging from the simple to very complex. VEGA uses sensors, transmitters, and switches with five main technologies to measure level in a multitude of different applications across at least a dozen key industries.
Solid Level Measurement Technologies
The technologies at VEGA are: radar, guided wave radar, vibration, capacitance, and radiometric. These different measuring methods detect level and convert that level into an electronic signal to be displayed directly on site or incorporated into a process control or management system. Each of these technologies has their pros, cons, and different price points. It comes down to what type of solid is being measured, what is happening inside the vessel, the vessel’s construction, the best technology for the application, and the customer’s preference.
Radar
How it works
Radar sensors send microwave signals toward the bulk solids being measured from above. The surface of the bulk solids below reflects the signals back in the direction of the antenna system. The instrument uses the time of flight for the microwave signals to determine a distance to the product surface, and then calculates a level inside using the known height of the tank, silo, or vessel.
VEGA Radar Sensors
VEGA’s radar sensors operate under three different frequencies: C-Band (5-8 GHz), K-Band (18-27 GHz), and W-Band (75-110 GHz). All three are used for continuous non-contact level measurement for all kinds of bulk solids. They can be used for bulk solids ranging in size from fine powders to large chunks, and are suitable for applications with stringent hygiene requirements.
Advantages
- Non-contact bulk solid measurement with high accuracy
- Measurement not affected by temperature, pressure, dust, or noise
- User-friendly adjustment saves time
- Accurate measurement without any moving parts
- Maintenance-free operation through non-contact measuring principle
Related products
Related applications
Crusher
Level measurement in the crusher
To be able to transport and further process the largest possible production volumes, the ore must have an optimal size. To achieve this, the ore is crushed to the correct size in two stages, in a primary and then a secondary crusher. In order to enable an optimum throughput, and avoid choking or damaging the crusher, a reliable level measurement is required.
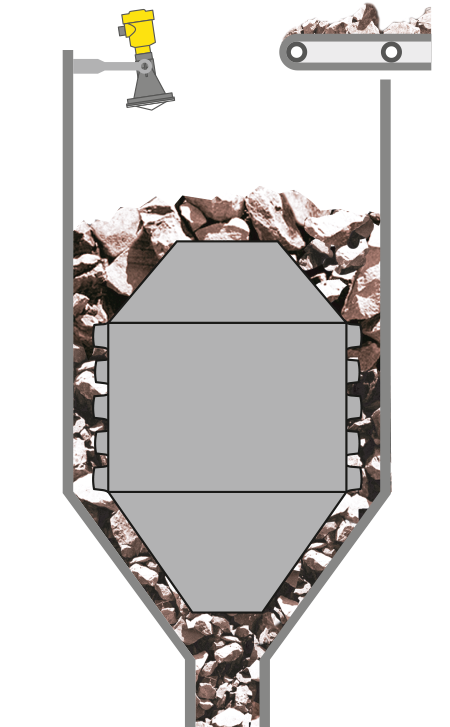
Reliable
Reliable measurement even during filling
Cost effective
Optimal utilization of the container volume
User friendly
Simple mounting and setup
Raw meal silo
Level measurement and point level detection in raw meal silos
Before being burned in the rotary kiln, the material from the blending bed and the aggregates are ground to a fine raw meal in large mills. The powdery material is then transported to the silo by a pneumatic conveyor system. Reliable monitoring of the level is essential for optimal raw material storage.
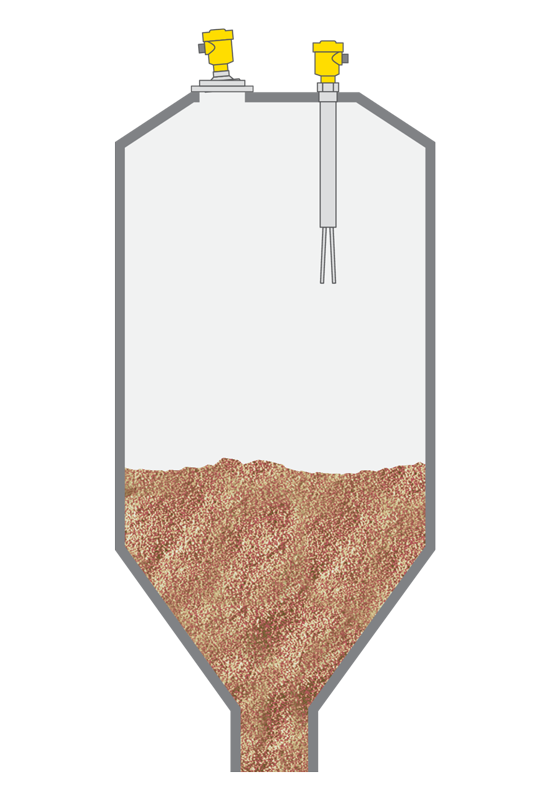
Reliable
Reliable measurement ensures a continuous supply of raw material
Cost effective
Optimal stocks ensure continuous production
User friendly
Maintenance-free operation
Conveyor belt
Mass flow measurement on conveyor belts
Bulk aggregates are fed into production processes via conveyor belts or screw conveyors. For effective feed control to and from these processes, or inter-production unit billing, the mass flow of the conveyed bulk material must be measured. A reliable belt-weighing scale system and mass flow rate ensures accurate measurement and smooth operation of the plant.
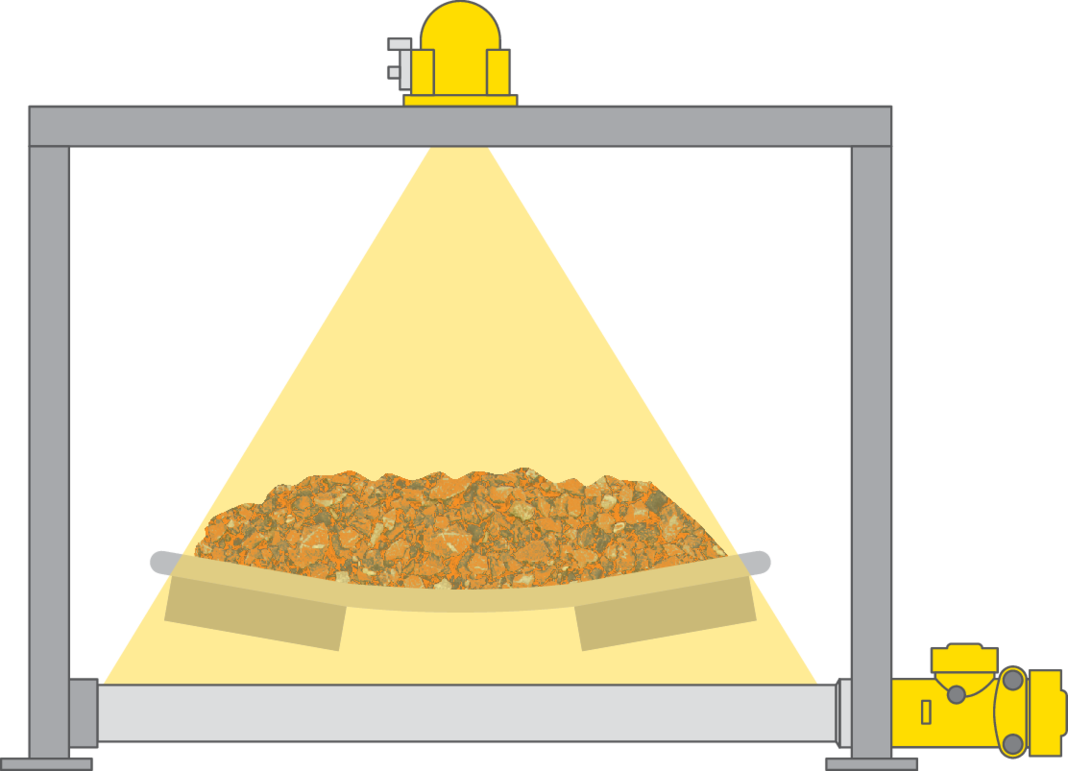
Reliable
Reliable measurement despite changing belt tension and vibrations
Cost effective
Optimal mass flow measurement allows exact accounting of bulk solids
User friendly
Maintenance-free operation
Guided Wave Radar
How it works
Guided wave radar sensors use time domain reflectometry to measure level. A cable or rod probe is mounted on top of the tank, silo, or vessel, and a low amplitude, high-frequency microwave pulse is sent down the probe to be reflected by the surface of the bulk solid. Once the pulse reaches the surface, a portion of the signal bounces back, and the amount of time it takes for the pulse to be transmitted and returned determines the level inside the tank, silo, or vessel.
VEGA Guided Wave Radar
The VEGAFLEX 82 can measure light and heavy-weight bulk solids even in the presence of dust and buildup. Two different probe options – cable or rod – ensure an accurate measurement for any range of bulk solids being measured.
Advantages
- Comprehensive diagnostic options ensure low-maintenance operation
- Shortenable probes enable simple standardization and maximum flexibility
- Measurements not affected by dust, noise, or varying dielectric constant
Related products
Related applications
Lime silo
Level measurement and high level detection in the lime silo
In the nitrogen and phosphorus removal stage, lime is used to stabilize the pH value. Stored in silos, the lime is added to the wastewater as a solid or as an aqueous suspension. The silo content is measured by a radar sensor and a point level sensor detects the maximum level and transmits a full signal.
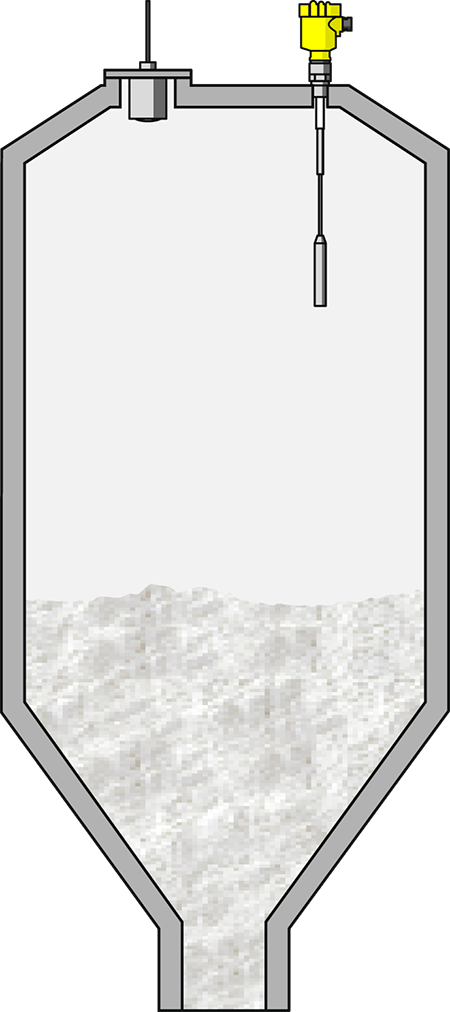
Reliable
Certain measurement even during filling
Cost effective
Reliable measurement of the total material volume in the silo
User friendly
Simple installation and setup
Medium-sized silos for bulk solids
Level measurement and point level detection in silos
Many different kinds of bulk solids are produced or used as raw materials in the chemical industry. To ensure reliable measurement of the silo contents, several factors must be considered: different bulk densities, abrasive properties, dust generation and the requirements of explosion protection. Application of the right level sensors ensures optimal production planning and reliable logistics for the finished products.
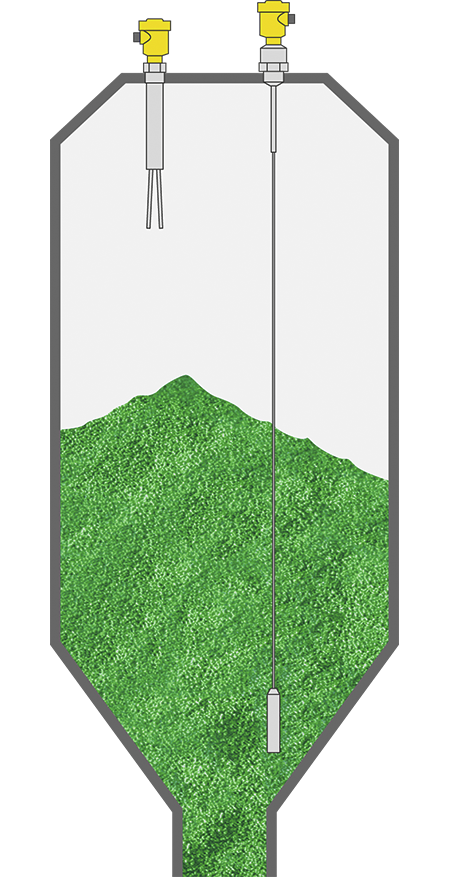
Reliable
Reliable measurement, independent of media properties and container geometry
Cost effective
Maintenance-free operation
User friendly
Universally applicable for almost all non-abrasive bulk solids
Vibration and Capacitance: Liquid Level Switching
How it works
Solid level switches detect when a certain predefined level is reached by the bulk solids inside a silo, tank, or vessel. These sensors are used when it’s not necessary to know where level is at every moment, like with continuous level measurement. A switch output can start or stop conveyors, sound an alarm, or simply turn on a light. Point level switches outputting a binary signal can be integrated into a process control system.
VEGA Switches
VEGA uses four different technologies for solid level switching: vibration, capacitance, microwave barrier, and radiometric.
Vibration switches, the VEGAVIB and VEGAWAVE series, are contact instruments that monitor vibration amplitude. These switches constantly vibrate at a specific amplitude. The amplitude changes once the solid reaches the vibration switch, and this change activates the output.
Capacitance switches, the VEGACAP series, are also contact instruments, but these measure capacitance in a system composed of the sensor, vessel, and the product inside. Once the solid reaches the sensor probe, there is a change in capacitance, and the switch output changes state.
Microwave barrier switches use two parts: a transmitter and a receiver. In between is an “invisible” barrier, and the switch is activated once that microwave barrier is broken or interrupted. These switches, called the VEGAMIP at VEGA, can provide “full” or “empty” options, and they can ignore product falling into a vessel.
Lastly, radiometric switches operate similarly in principle to microwave barrier switches, but these instruments use gamma radiation emitted from a source holder while a detector measures the amount of radiation reaching it. Unlike any of the previously mentioned switches, radiometric switches can be installed completely externally, which is why they’re typically used to measure harsh or volatile processes like those seen in the paper industry, mining, and building materials.
Advantages
- Minimum or maximum detection with low maintenance costs
- Vibration switches are simple plug and play instruments
- Microwave barrier switches offer simple adjustment
- Radiometric switching is completely non-contact
Related products
Related applications
Large storage silos
Level measurement and point level detection in large storage silos
To ensure continuous production, even if material production is interrupted, the raw materials are stored in large bunkers with heights of over 30 m and diameters of up to 20 m. The large dimensions of the silos require the filling and emptying to take place at multiple points. Uniform filling and emptying of the bunkers is achieved through level measurement at various points in the bunker.
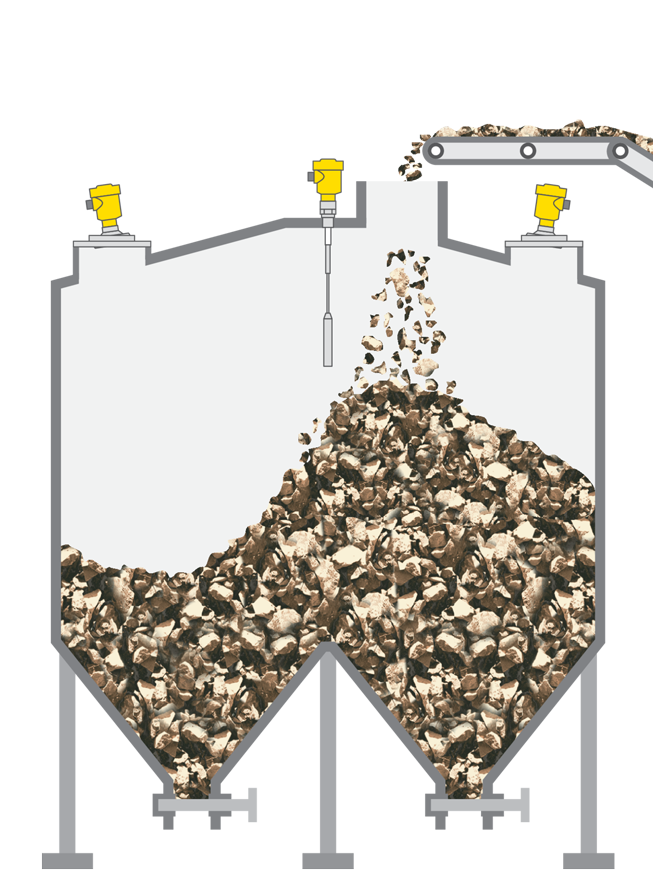
Reliable
Reliable measurement even in dusty and noisy environments
Cost effective
Optimal filling of the silos
User friendly
Maintenance-free operation
Buffer tank
Buffer tank pressure measurement and point level detection
In the smelter, above the fused salt electrolysis bath there are small buffer tanks that are pneumatically fed via pipelines. The alumina powder is dispensed into the melt bath in small quantities from these tanks. The filling of the buffer tank is controlled by the feed pressure. Full and empty alarms ensure optimal charging of the powder.
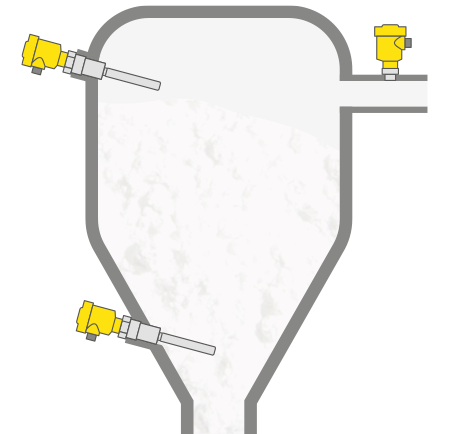
Reliable
Reliable function under all operating conditions
Cost effective
Simple installation into existing vessels
User friendly
Maintenance-free operation
Bulk solids stockpile
Level measurement of stockpiles
After being crushed, screened and sorted into different grain sizes, the gravel and sand are transported on conveyors and stored in large stockpiles. To automate the stockpiling levels and enable the optimum area to be filled, a reliable level measurement is essential.
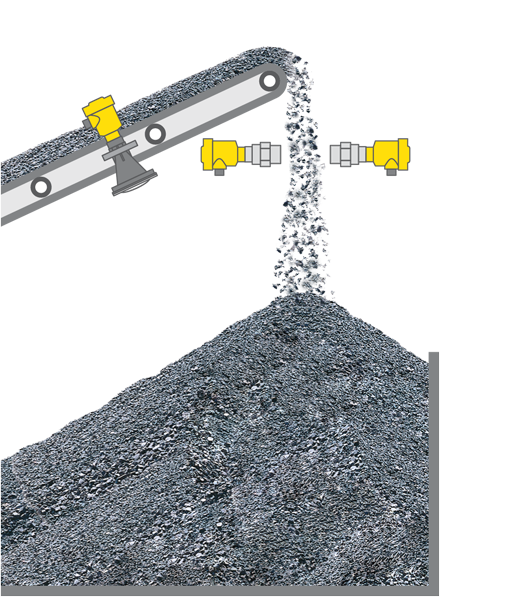
Reliable
Reliable measurement is ensured in all weather conditions
Cost effective
Optimum utilization of stockpile capacity
User friendly
Maintenance-free operation
Radiometric
How it works
Radiometric level measurement sounds complicated, but the principle behind it is relatively easy to understand. Gamma radiation emits from a source holder, and a detector measures the radiation that reaches it. The amount of energy reaching the detector will vary based on the amount of solids inside the tank, silo, or vessel. The electronics inside the detector use the gamma reading to infer a measurement and output the value.
VEGA Radiometric Sensors
The ProTrac Series is used for continuous level and point level monitoring in the most difficult bulk solids applications because they measure without contacting the process material. This means there is no chance of damaging the detectors with harsh, abrasive, or corrosive products that would require frequent and expensive maintenance. Plus, these instruments are impervious to thermal shock, drastic pressure shifts, and other extreme process conditions.
Advantages
- Maximum operational reliability even in the harshest environments
- Measurement is independent of pressure, temperature, and product aggressiveness
- Measuring system can be installed on the outside of a vessel during ongoing production
- Retrofitting is made easy through a family of adapter brackets
Discover the right radiometric instrument for your application
Related products
Related applications
Cyclone
Buildup measurement in cyclones
In clinker production, cyclones are used to preheat the raw meal. Before the raw meal enters the rotary kiln it is preheated to +900 °C in the cyclone. Constant monitoring of the buildup thickness on the walls ensures a continuous process.
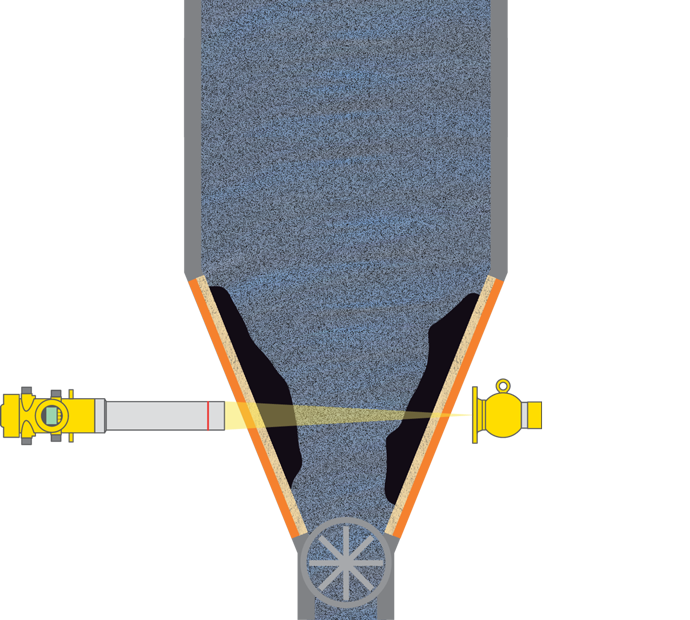
Reliable
Reliable buildup measurement despite high temperatures
Cost effective
Monitoring the formation of buildup ensures high availability of the cyclone
User friendly
Simple external mounting
Digester
Level detection and pressure measurement in the digester
In the digester, the action of chemical dissolution removes the lignin binder, thereby exposing and freeing the cellulose fibres. During the cooking process according to the alkaline sulphate method, the fibres are fed into the digester by means of steam pressure. To enable fully automatic operation of the digester, a point level detection of the filling is required. The vessel pressure also needs to be carefully monitored throughout this process.
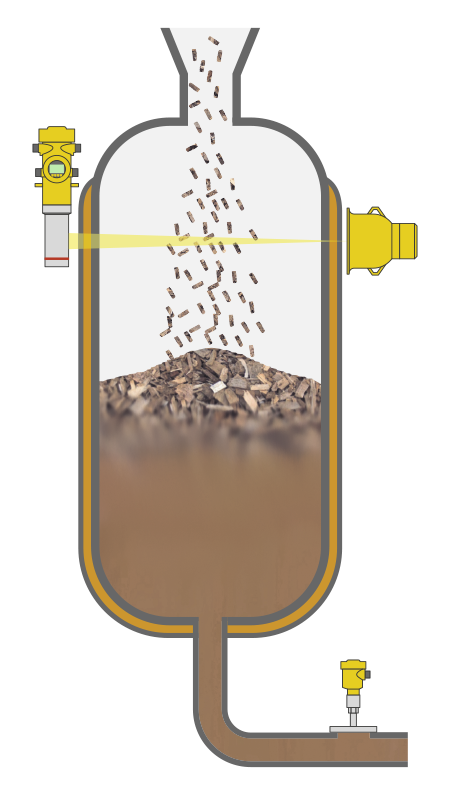
Reliable
Reliable operation despite extreme process conditions
Cost effective
Measuring system can be installed without invasive work on the vessel wall and insulation
User friendly
Simple retro installation
Continuous catalyst regeneration
Level measurement and point level detection of catalyst
Platformers and reformers, both catalyst-based processes, require “fresh” catalyst at a given point in their cycle. To provide fresh catalyst without shutting down the process, a continuous catalyst regeneration unit can be installed. This unit regenerates the spent catalyst so that it can be used again. Maintaining the proper level in the vessel ensures that the expensive catalyst is used at the highest level of efficiency without waste.
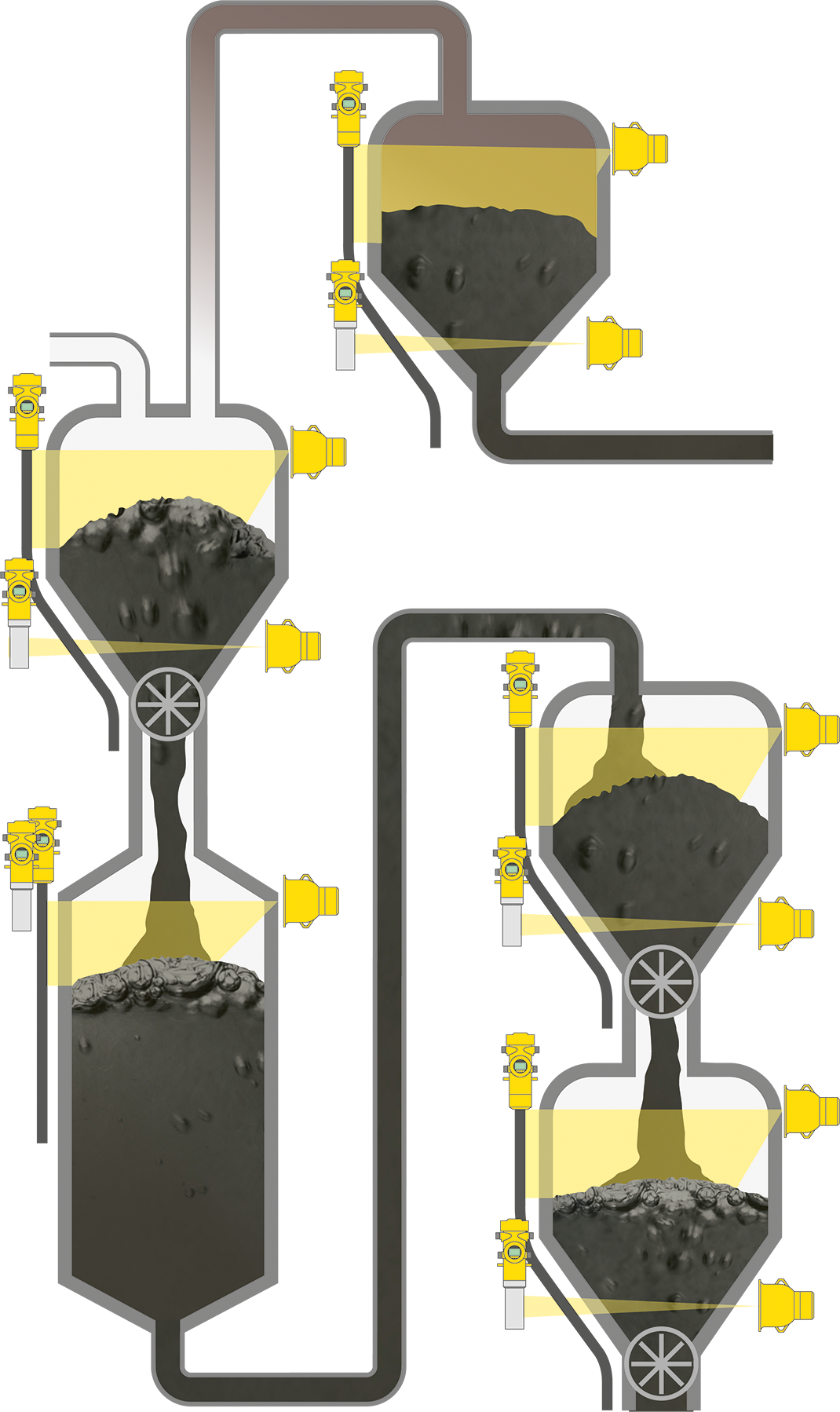
Reliable
Non-invasive measurement ensures high plant availability
Cost effective
Lightweight design reduces mounting costs
User friendly
External mounting does not interrupt the process
Export this article
Download as PDFShare this article
Comments ({{comments.length}})
{{getCommentAuthor(comment, "Anonymous")}} {{comment.timestamp | date : "dd.MM.yyyy HH:mm" }}
{{comment.comment}}