Monitoring the level of molten polyethylene for car parts
More than ever before, a good portion of our cars are made from plastics and plastic composites. According to the American Chemistry Council, plastics account for approximately 50 percent of the volume of a typical vehicle. Using plastic in cars helps achieve better fuel efficiencies and improves vehicle safety. Many times, these plastic parts are made of polyethylene, and recently, VEGA Americas helped an auto parts manufacturer track the level in their tanks.
Making a measurement in the tightest of spaces
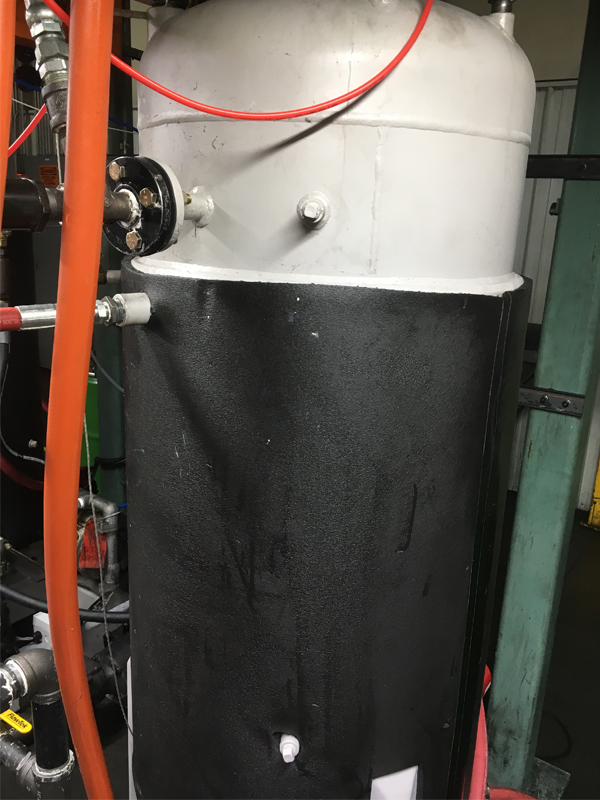
Creative mounting made possible with the VEGAPULS 64
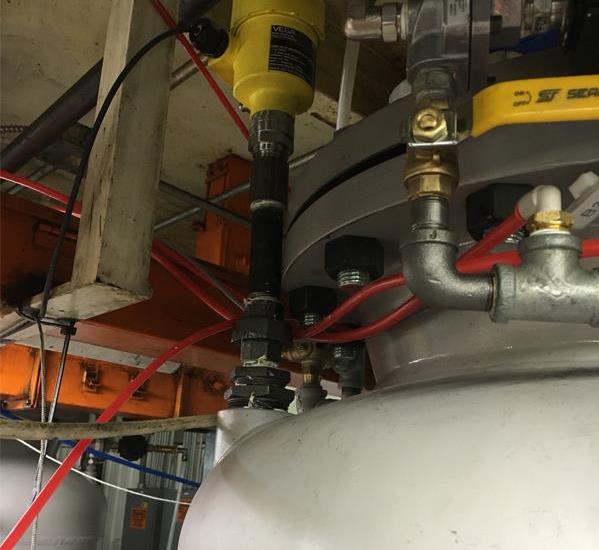
Mounting on sockets
We need your consent
This content is provided by an external provider. If you activate the content, personal data may be processed and cookies set.
A solution worth repeating
Find out more about the capabilities of 80 GHz radar:
Export this article
Download as PDFShare this article
Comments ({{comments.length}})
{{getCommentAuthor(comment, "Anonymous")}} {{comment.timestamp | date : "dd.MM.yyyy HH:mm" }}
{{comment.comment}}