VEGA sensors under extreme pressure
The TDR sensor VEGAFLEX 86 handles the challenging measurement situation successfully in a nuclear power station in China.
The gas separation system is considered the key system between the high and low pressure turbines of a 1000 MW nuclear power plant in China. Steam from the high-pressure turbine contains 14% moisture, which makes it necessary to first dehumidify the steam before it is fed into the low-pressure turbine. This steam is then heated again. The condensate is collected and treated in tanks with drains. The condensate tanks play an important role in the gas separation system. The water in the waste water tank must not exceed a certain level. Because: if the tank is too full, there is a risk of water entering the gas separation system, which in turn increases the water content of the steam and thus the likelihood of damage to the low pressure turbine. The level measuring instruments installed there thus perform an important task for safe and efficient operation of the gas separation system and the turbines.
In the 2-meter-diameter spherical tanks the operating conditions are extreme:
- process temperature 280° C
- pressure 66 bar
- previous level instrumentation: guided radar sensors from another manufacturer
- three level transmitters per tank operating in a 2-out-of-3 selection circuit
With this system, the average value of the three measurements was output as the level in the tank. The three measuring instruments were installed directly in the vessel instead of in bypass tubes.
Related applications
Condensate storage tanks
Level measurement and point level detection in condensate storage tanks
Throughout the different process units, there are storage vessels that collect clean, reusable condensate. This condensate accumulates from the steam system that is used to heat the various hydrocarbon processes. The condensate tanks routinely have extremely high process temperatures, so a level measurement and point level detection are necessary that can withstand this environment.
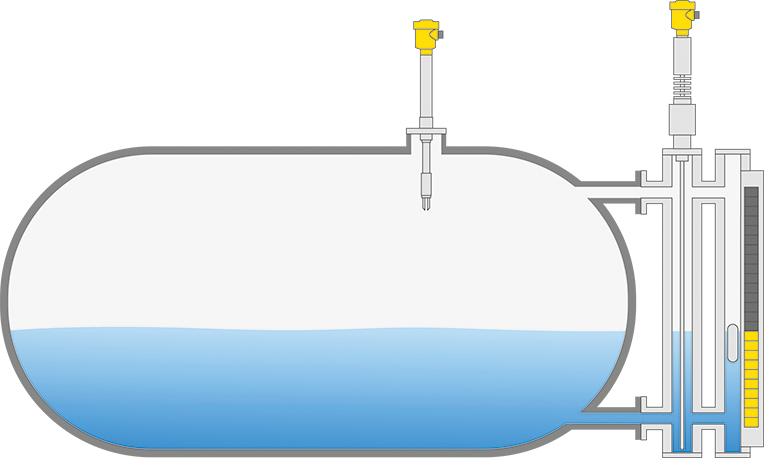
Reliable
Safe measurement unaffected by high temperature and steam
Cost effective
Maintenance-free through optimal redundancy arrangement
User friendly
Simple setup and installation
Sensors have to withstand high pressure and high process temperatures
❗ First weak point: the spacers
These are necessary, as otherwise when there is strong vibration or a mechanical impact the rod probe would touch the coaxial tube, which in turn would lead to erroneous measured values. These spacers were made of PEEK and were repeatedly attacked by the hot steam, becoming brittle and finally breaking. There was always the risk that parts of the spacers would break off and find their way into the steam system and thus endanger the safe and reliable operation of the turbine. The operator managed to keep things going by replacing the coaxial probe every time the turbine was serviced.
❗ Second weak point: the seal between the process and the sensor
The steam penetrated the sealing system and entered the sensor housing. This damaged the instrument again and again. In retrospect it turned out that the O-ring seal of the sensor could only withstand temperatures up to 150° C and the temperature limit for PEEK insulation material was 250° C. Both temperature limits were thus significantly lower than the process temperature of 280° C.
The dielectric constant changes according to the pressure and temperature of the medium. Steam has a higher dielectric constant than air. As a result, the propagation speed of microwaves in steam decreases. The measuring instrument thus indicates a lower level than is actually present. Although this measurement error was compensated for, the result was simply not accurate enough.
The measurement deviation of the three field instruments at the start of the process was always less than 20 mm, but this only applied in the cooled-down state. As soon as the turbine system was activated and the process temperature and the pressure in the condensate tank increased, the measurement deviations gradually increased and were up to 100 mm or more. Here, too, the operator resorted for many years to a workaround that involved correcting the measured value each time the deviation became too great.
Guided radar sensor VEGAFLEX as problem solver
Still, the operator was not satisfied with this and started looking for another solution.
👍 The responsible engineers found what they were looking for when they came across VEGAFLEX 86, a level transmitter with steam compensation. This robust sensor for continuous level and interface measurement of liquids has established itself especially in applications with extreme temperature and pressure conditions. The device has ceramic insulation and a graphite seal in the coupling that can withstand the penetration of steam at a pressure of up to 400 bar and a temperature of up to 450° C.
A good solution to the problem of fluctuating dielectric constant has also been developed for this guided radar sensor: an innovative steam compensation system. This vastly improves measurement accuracy. VEGAFLEX 86 uses a reference distance to compensate for the deviation caused by high-pressure steam. The longer this distance, the more accurate the measurement. VEGAFLEX 86 has the longest reference distance on the market. We need your consentThis content is provided by an external provider. If you activate the content, personal data may be processed and cookies set.
Related industries
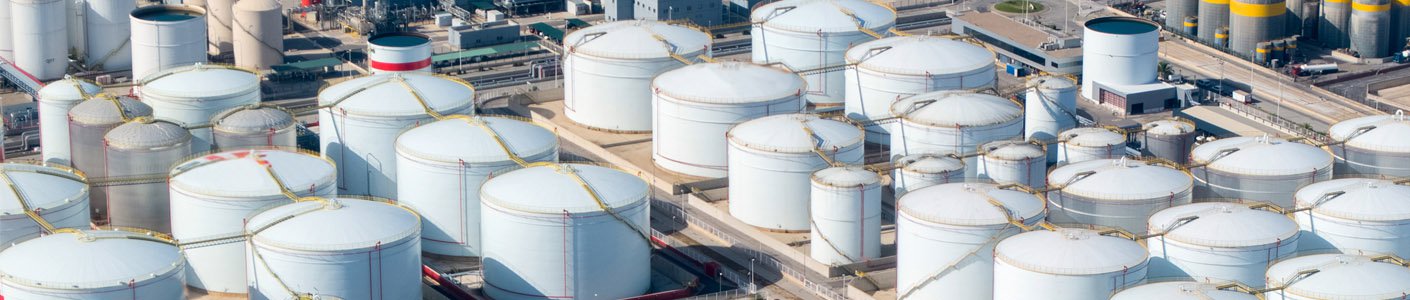
Refining and petrochemical
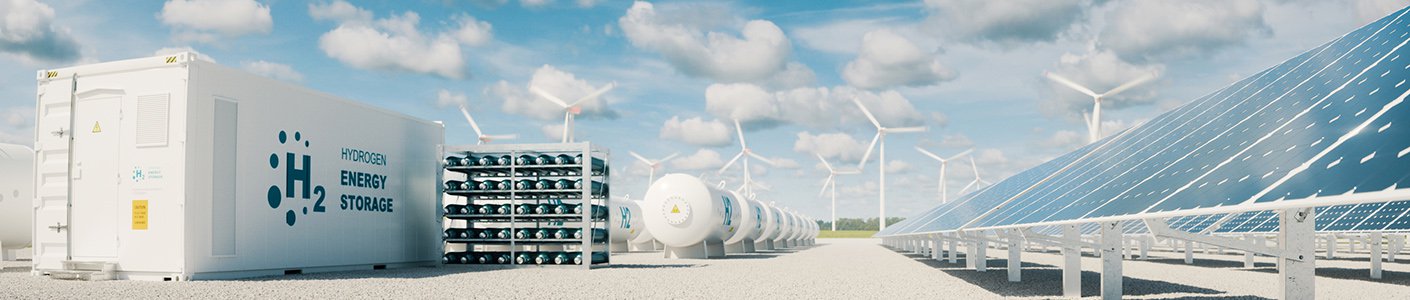
Energy
Related products
Export this article
Download as PDFShare this article
Comments ({{comments.length}})
{{getCommentAuthor(comment, "Anonymous")}} {{comment.timestamp | date : "dd.MM.yyyy HH:mm" }}
{{comment.comment}}