Measurement technology secures hydrogen processes
Hydrogen is the key element for a greener economy. Hardly any other area of the global economy is currently experiencing so much development and dynamism. Research, trials and tests are being conducted worldwide. No matter which technology ultimately prevails, one thing is certain: Reliable measurement technology is essential in hydrogen processes. VEGA’s measuring instruments are already making an important contribution to the safe handling of hydrogen.
In this interview, VEGA Product Managers Stefan Kaspar and Robin Müller discuss the most important aspects of hydrogen, highlight the many possible applications of the sensors for level, switching and pressure and look ahead to an exciting future.
Hydrogen is seen as a decisive factor in the energy transition. Why?
Robin Müller:
Hydrogen is an amazing element. If it is produced using electricity from renewable energy sources, it is a green energy source. When it releases this energy, the only “waste product” generated is water – no environmentally harmful emissions. The entire life cycle of hydrogen – from production to consumption – is completely CO2 neutral. For that reason, there is huge potential in hydrogen.
Stefan Kaspar:
Hydrogen has been used for a long time already. In the chemical industry, for example, it has been used as a precursor as well as intermediate product for many years. Until now, it has been generated mostly by steam reforming of fossil fuels such as natural gas – which is why it is referred to as grey hydrogen, because large quantities of CO2 are also produced in the process. But within the context of climate protection, it is green hydrogen, produced with renewable energy, that’s becoming more important. It could significantly reduce the CO2 footprint of energy-intensive processes such as those found in steelworks or refineries.
What role does reliable measurement technology play in the handling of hydrogen?
Robin Müller:
Green hydrogen is extremely high-priced, as its production is still relatively expensive. It is therefore immensely important that processes run efficiently, safely and, above all, with no hydrogen escaping. From production to transport to utilisation, measurement technology helps to ensure that as little as possible of this valuable energy carrier is lost.
Where exactly is measurement technology used in hydrogen processes?
Stefan Kaspar:
Sensors for level and pressure ensure safe and efficient processes along the entire hydrogen value chain. A good example is the alkaline electrolyser, where precise measurement is required at many points. Reliable level and pressure data is needed virtually everywhere – in storage tanks for the electrolyte, in the water and oxygen pipelines, in the compressor and finally in the intermediate storage tank, where hydrogen is present in gaseous form.
Robin Müller:
Whether for switching or level, differential pressure or simple pressure monitoring – our measurement technology is crucial for the efficiency of hydrogen processes.
What other challenges does hydrogen pose?
Robin Müller:
Diffusion is of course always an issue with hydrogen. And hydrogen embrittlement is also something that needs to be considered, especially at high pressures and temperatures. Our instrumentation is designed for both – with resistant stainless steel such as 316L and diffusion-tight, high-pressure fittings, the sensors meet the special requirements and are very stable over the long term.
Stefan Kaspar:
We also offer our metallic pressure measuring cells with gold as well as gold-rhodium coatings. There is no better protection against diffusion.
How exactly do VEGA sensors fulfil these high requirements?
Stefan Kaspar:
Aggressive media, high pressures, extreme temperatures or gaseous oxygen and hydrogen overlays – our measurement technology has to be able to cope with all these challenges. And cope it does – brilliantly! VEGAFLEX and VEGAPULS 6X radar sensors, among others, are very much in demand for level measurement in hydrogen applications. They also measure media with a low dielectric constant and are easy to clean. This is particularly important where the sensors are used in an oxygen atmosphere, for example in electrolysers. They meet the common global standards ASTM G93 and EIGA 33/18.
Robin Müller:
Different instruments are used for pressure measurement depending on the application. Two examples: VEGABAR 83 with dry strain gauge measuring cell ensures long-term stable measurement at high process pressures up to 1000 bar. With its oil-free ceramic measuring cell, VEGABAR 82 can also withstand aggressive media such as potassium hydroxide, and thanks to its high overload capacity, it is just the right sensor for many processes in hydrogen production.
Safety is always the buzzword when it comes to hydrogen. Why is that so?
Stefan Kaspar:
Hydrogen and oxygen together can form an explosive mixture. However, hydrogen production and transport are much less dangerous than people generally think. Electrolysers have exhaust air systems that move hydrogen – should it accidentally leak out – to the outdoors so that an explosive hydrogen-oxygen concentration does not arise in the first place. Nevertheless: Safety is the top priority when handling hydrogen. Our sensors for these applications therefore have Ex and SIL qualifications.
What trends can we expect to see in the coming years?
Stefan Kaspar:
There are currently many exciting projects underway and it remains to be seen which technologies will ultimately prevail. At the forefront are the sectors and industries that already work with hydrogen, such as the chemical and steel industries. Many companies are currently building their own electrolysers in order to gain initial experience – but at present they can only cover a small proportion of the demand. There are also national subsidy programmes in many countries around the world. It will be interesting to see what developments occur in sectors where hydrogen is not yet widely used – for example the transport industry. Hydrogen has great potential as a propellant for heavy goods vehicles or trains.
Robin Müller:
There are still many questions regarding international supply chains in the hydrogen economy. How does hydrogen produced in countries with a lot of renewable energy from wind or solar get to other parts of the world? Will it be liquified for transport or first converted into ammonia, e-fuels or methanol? It might be another ten to 20 years before we know the answers to these questions. But one thing is already certain: Our measurement technology is just right for this industry.
Related industries
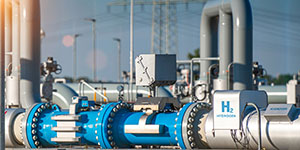
Hydrogen
Products
Export this article
Download as PDFShare this article
Comments ({{comments.length}})
{{getCommentAuthor(comment, "Anonymous")}} {{comment.timestamp | date : "dd.MM.yyyy HH:mm" }}
{{comment.comment}}