Des capteurs VEGA sous pression
Le capteur VEGAFLEX 86 réponds parfaitement aux situations de mesures exigeantes dans une centrale nucléaire en Chine.
Dans une centrale chinoise, dotée d'une capacité de 1000 MW, le système de séparation des gaz est un composant clé entre les turbines haute et basse pression. La vapeur de la turbine haute pression contient 14 % d'humidité et doit donc être asséchée avant d'être envoyée dans la turbine basse pression. Puis cette vapeur est à nouveau chauffée. Le condensat est collecté et traité dans des réservoirs équipés d'un écoulement. Ces réservoirs de condensat jouent un rôle important dans le système de séparation des gaz. Dans la cuve des eaux usées, le niveau ne doit pas dépasser une valeur donnée. En effet, si la cuve est trop pleine, il y a un risque que de l'eau pénètre dans le système de séparation des gaz, ce qui augmente l'humidité de la vapeur et risque d'endommager la turbine basse pression. La mesure de niveau installée sur cette cuve assure donc une mission cruciale pour garantir le fonctionnement sûr et efficace du système de séparation des gaz ainsi que des turbines.
Dans cette cuve conique de 2 m de diamètre, les conditions sont extrêmes :
- température de process à 280 °C
- pression à 66 bar
- instrumentation de mesure précédemment utilisée : capteurs radar à ondes guidées d'un autre fabricant
- trois capteurs par cuve, fonctionnant en combinaison redondante 2/3
La moyenne des trois mesures de niveau a été utilisée par le système pour déterminer le niveau de la cuve. Les trois capteurs étaient installés directement dans la cuve, sans tube bypass.
Applications
Réservoir de condensat
Mesure et détection de niveau dans un réservoir de condensat
Les condensats propres et réutilisables sont collectés dans des réservoirs. Ce condensat provient du système de vapeur, qui sert à réchauffer les différents processus de traitement des hydrocarbures. Les températures élevées. dans les réservoirs de condensats nécessitent un système de mesure et de détection de niveau adapté à ces conditions.
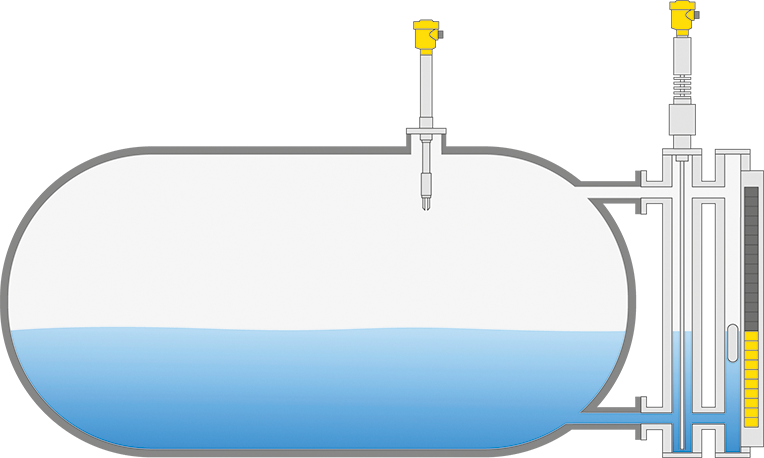
Sûr
Mesure sûre, indépendamment de la température élevée et de la vapeur
Économique
Sans maintenance grâce au système redondant optimal
Confortable
Mise en service et installation simples
Les capteurs doivent supporter une forte pression et une température process élevée
La pression élevée de la vapeur, en particulier, a causé quelques difficultés. À haute vitesse, même les plus petites gouttes d'eau peuvent développer une puissance énorme et attaquer de nombreux matériaux. Dans cette application également, la vapeur causait régulièrement des problèmes en différents endroits.
❗ Point faible n° 1 : les entretoises
Elles sont nécessaires pour éviter que la sonde tige ne touche le câble coaxial en cas de vibrations ou de chocs mécaniques, ce qui provoquerait des sauts dans les valeurs de mesure. Ces entretoises en PEEK ont été attaquées par la vapeur à plusieurs reprises, devenant ainsi friables et finissant par se briser. Le risque étant que des morceaux d'entretoises pénètrent dans le circuit de vapeur et compromettent le bon fonctionnement de la turbine. Pour y remédier, on changeait la sonde coaxiale à chaque maintenance de la turbine.
❗ Point faible n° 2 : l'étanchéité de l'appareil
La vapeur pénétrait dans le joint d'étanchéité et parvenait jusqu'au boîtier. Par conséquent, l'instrument de mesure était souvent endommagé. Avec le recul, il s'est avéré que le joint torique de l'appareil ne résistait qu'à des températures maximales de 150 ℃ et le matériau isolant en PEEK de 250 C. Or, la température process atteint 280 ℃, ce qui est nettement plus élevé.
Par ailleurs, la constante diélectrique varie en fonction de la pression et de la température. La vapeur possède une constante diélectrique supérieure à celle de l'air. Par conséquent, la vitesse de propagation des micro-ondes diminue dans la vapeur. L'appareil indique donc un niveau inférieur à la réalité. Cet écart de mesure était compensé, mais de manière insuffisante.
Au démarrage du process, l'écart de mesure des trois appareils de terrain était toujours inférieur à 20 mm, mais cela ne s'appliquait qu'à l'état refroidi. Dès que les turbines étaient activées et que la température process et la pression augmentaient dans la cuve de condensat, les écarts de mesure augmentaient progressivement et pouvaient atteindre 100 mm ou plus. Là aussi, pendant des années, on s'est contenté d'une solution temporaire consistant à corriger la valeur mesurée à chaque fois que l'écart devenait trop important.
Capteur radar à ondes guidées VEGAFLEX : la solution idéale
Pour l'exploitant, cette situation n'était pas satisfaisante et il a commencé à rechercher une autre solution.
👍 Il l'a trouvée chez VEGA avec le VEGAFLEX 86 avec compensation de la vapeur. Ce capteur robuste pour la mesure continue de niveau et d'interface des liquides a fait ses preuves dans les conditions extrêmes de température et de pression. L'appareil dispose d'une isolation en céramique et d'un joint en graphite dans le raccord, capables de résister à la pénétration de vapeur à une pression de 400 bar et une température de 450 °C maximum.
Ce capteur radar à ondes guidées est également une bonne solution pour les variations de la constante diélectrique. Un système innovant de compensation de la vapeur garantit une précision de mesure accrue. Le VEGAFLEX 86 utilise une distance de référence qui lui permet de compenser l'écart de mesure causé par la vapeur à haute pression. Plus cette distance est longue, plus la mesure est fiable. Le VEGAFLEX 86 dispose de la plus longue distance de référence du marché. We need your consentThis content is provided by an external provider. If you activate the content, personal data may be processed and cookies set.
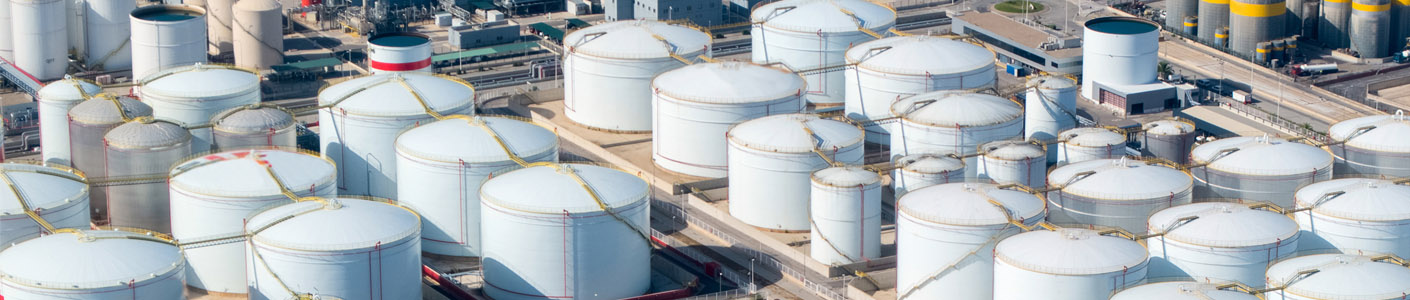
Raffinerie et pétrochimie
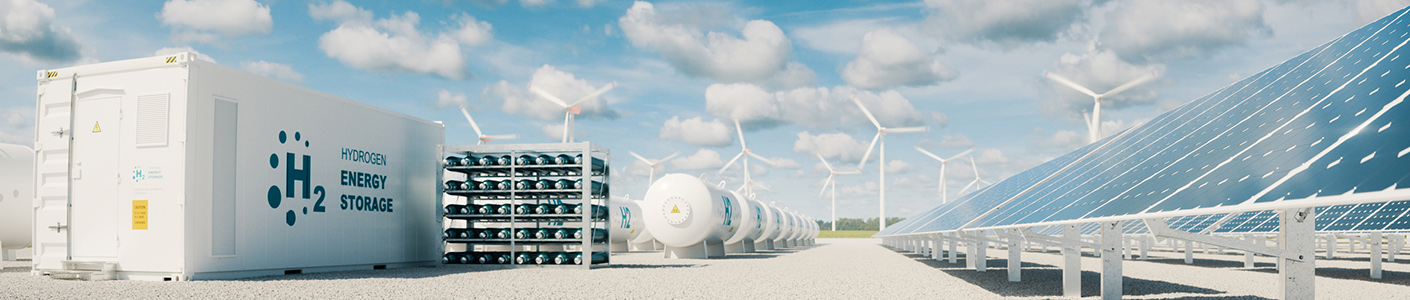
Production d’énergie
Mesure et détection de niveau et de pression dans tous les process de production d'énergie.
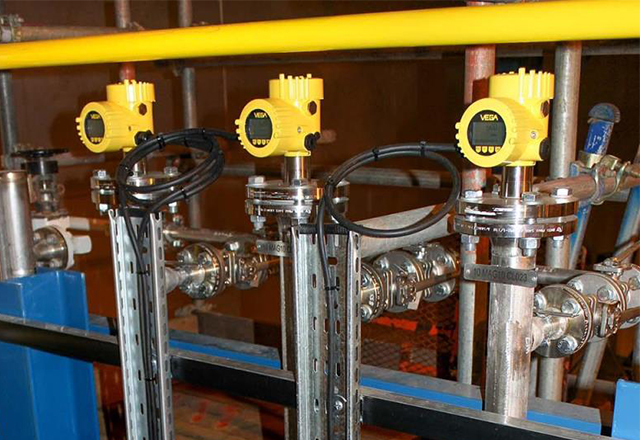
Une centrale à l'équilibre grâce au VEGAFLEX 81
Lire la suite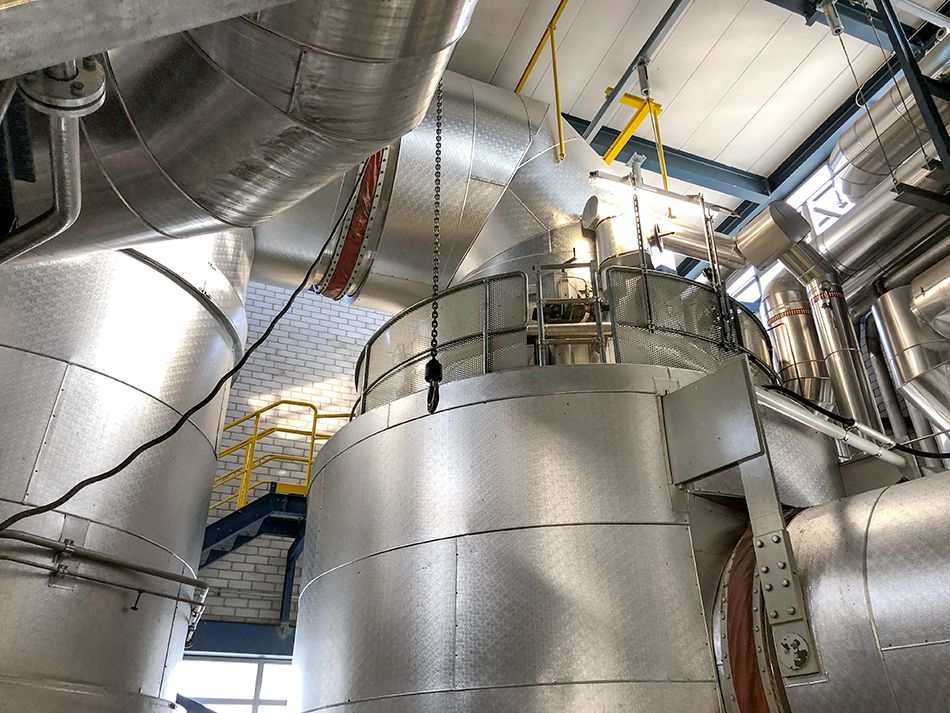
Capteur radar à ondes guidées VEGAFLEX : à toute vapeur pour une alimentation efficace en chaleur
Lire la suiteExporter cet article
Télécharger en PDFPartager cet article
Commentaires ({{comments.length}})
{{getCommentAuthor(comment, "Anonyme")}} {{comment.timestamp | date : "dd.MM.yyyy HH:mm" }}
{{comment.comment}}