Density measurements with radiometric technology explained
Industrial processes have been using radiometric technology for challenging density measurements since the 1950’s. In the past 70 years, this technology has gone by many names – nuclear, nucleonic, and radiation-based to name a few – and the engineers working on it have made countless improvements to the safety and accuracy of the technology.
Facilities use radiometric sensors for their all-important density measurements because of the non-intrusive nature of the technology. For processes reliant on knowing the contents of pipelines and vessels, knowing the density can help operators make informed decisions. This paper will outline how radiometric density sensors work, their advantages and limitations, and discuss some of the most common applications where these sensors are used.
Advantages of radiometric density sensors
Radiometric technology is used for density measurements because these sensors make a measurement without contacting the process material. A non-contact measurement ensures a wear- and maintenance-free operation. Abrasive, harsh, or corrosive products oftentimes result in frequent and expensive maintenance or replacements for other sensors, but radiometric density detectors can last for upwards of 20 to 30 years.
The source holder and the detector are both mounted on the outside of the pipe or vessel, so the system is immune to buildup, thermal shock, drastic pressure shifts, or other extreme process conditions. And because of their robust design, radiometric instrumentation is able to withstand vibrations from the pipe or vessel where it’s mounted.
Installing these radiometric sensors is much simpler compared to other technologies. Brackets and instrumentation can be mounted without an expensive process shutdown. Other technologies require sections of pipe to be removed or other significant alterations to the process itself.
Source holders, while heavy, are easy to mount and install. Detectors are lightweight and can be mounted in a variety of positions to optimize the measurement. Additionally, modern detectors are smaller and more sensitive than their predecessors, so newer detectors can easily be retrofitted with older source holders that may output less gamma energy than when they were first installed.Limitations to radiometric technology
The MiniTrac 31 is immune to dusty conditions at a cement plant and continues to output an accurate density measurement in a vertical pipe.
The sale of radioactive material is highly regulated, and rightfully so. These extra regulatory burdens prolong the buying process because companies need to obtain the appropriate licenses, and personnel need to complete required training courses. Fortunately, radiometric instrumentation suppliers like VEGA have entire departments dedicated to assisting customers with licensing, safety training, and auditing radiation safety programs.
Beyond the regulatory costs, the initial material cost of radioactive isotopes is higher than other density measurement solutions. However, a radiometric solution can last 20 or 30 years with little to no maintenance. Unlike other solutions, radiometric density sensors are a long-term investment in the entire process, keeping it running safely and efficiently for decades to come. A single radiometric density sensor provides dramatic operational cost-savings over the life of the instrument.
Common applications for radiometric density sensors
A variety of industries use radiometric technology for density measurements. Mines, paper mills, coal power plants, building material manufacturers, and oil and gas operations all use this technology for density measurements somewhere in their processes. Whether the output is a density measurement, a percentage of solids, or API, radiometric density detectors can be found in some of the most challenging environments of heavy industry.
By working closely with customers, VEGA designed and developed innovative new ways to use density measurements to better control processes in challenging applications. For example, VEGA devised a way to use multiple density sensors on a single vessel to give operators a better view of different fluid layers.
The multi-point density array, or MDA, is commonly found on separator vessels in refineries. The crude oil, water, and interface layer in between all have different densities, and with multiple density measurements, operators have better control of each layer. Plus, the externally mounted, non-contact radiometric technology is immune to the buildup issues of other intrusive solutions.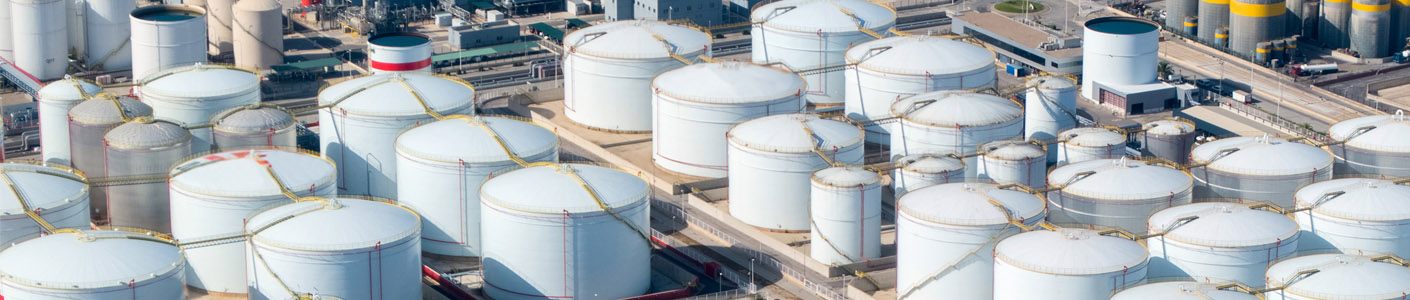
Rafinacja i petrochemia
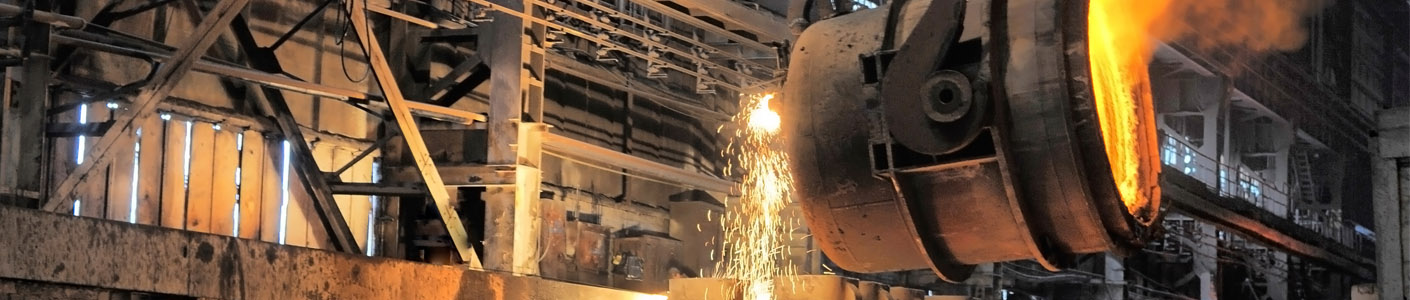
Wydobycie i przetwórstwo rud metali
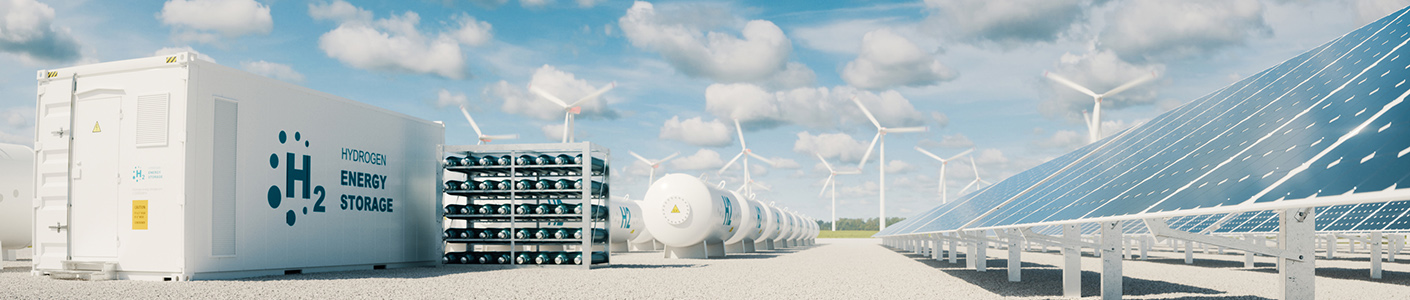
Energia
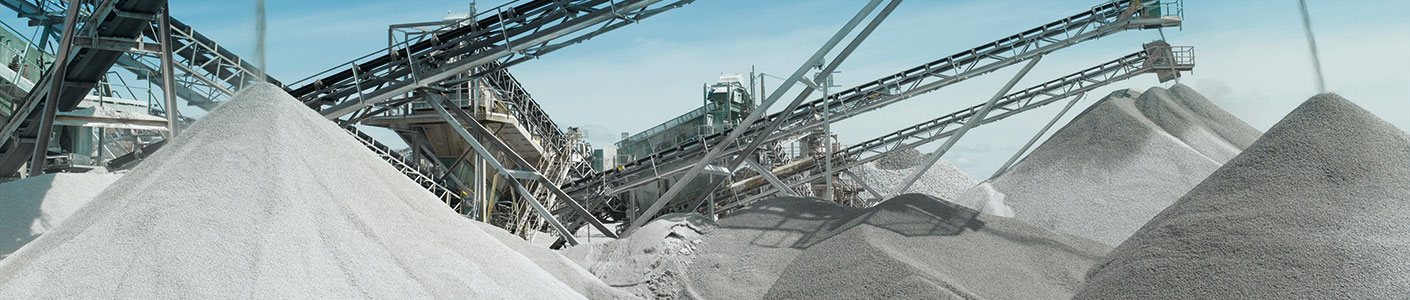
Materiały budowlane
Conclusion
Density measurements give operators a better understanding of their processes, helping them optimize throughput of a slurry through a pipe, identify blockages, and even improve control in complex applications. Radiometric density sensors are non-contact, which means they don’t interfere with the process, and they’re wear- and maintenance-free, allowing them to last longer. External mounting makes installation easy, even when retrofitting new detectors with older sources.
These instruments have a lot to offer users willing to accept the regulatory and financial responsibilities. After all, radiometric density sensors are more of a long-term investment than most other instrumentation. For challenging and vital density measurements, radiometric technology has delivered reliable results for more than half a century.Eksportuj ten artykuł
Pobierz jako PDFUdostępnij post
Komentarze ({{comments.length}})
{{getCommentAuthor(comment, "Anonim")}} {{comment.timestamp | date : "dd.MM.yyyy HH:mm" }}
{{comment.comment}}