Safety, hygiene and quality management – VEGA sensors fulfil the requirements of the pharmaceutical industry
VEGA offers the entire range of suitable measuring principles for level and pressure. The advantages of the sensors:
- Standardised process fittings
- Standardised hygienic adapter system
- Diffusion-tight
- Extremely robust
- Designed for CIP and SIP processes
The following examples show which tasks the sensors perform and where they are used.
Level measurement sensors:
The radar sensor VEGAPULS 42 is particularly suitable when continuous automation is required for rapid level changes.
With its versatile, hygienic adapters, it meets the processes requirements with high levels of hygiene. VEGAPULS 42 with IO-Link ensures ideal networking of process data with the user’s business administration and laboratory systems. The sensor’s non-contact, 80-GHz radar technology enables maintenance-free operation.
It measures at a distance of up to 15 metres and at temperatures of up to 150 °C. This makes it ideal for use in dosing systems or in downstream process steps, such as conveyor systems and filling systems, for example.
VEGAPULS 6X
The radar sensor VEGAPULS 6X, with its exceptionally high measurement accuracy, is the right choice for particularly challenging conditions. Thanks to the strong focussing of the radar beam, tank installations such as agitators do not impair the sensor’s ability to measure reliably. With its high dynamic range, VEGAPULS 6X still reliably measures products containing oil, solvents or other media with poor reflective properties.
Pressure measurement sensors:
Fast reaction times are crrucial characteristics when it comes to supply lines carrying heating media. The VEGABAR 28 pressure transmitter enables reliable pressure monitoring of gases, vapours and liquids at up to 130 °C. Its ceramic-capacitive CERTEC® measuring cell, developed and produced by VEGA itself, has a lot to offer: It is abrasion-resistant, oil-free and demonstrates high long-term stability and a high overload capacity. For users, the optional universal fitting for hygienic adapters on VEGABAR 28 reduces installation costs and the stocking of spare parts.
Point level sensors:
Reliable detection and a long service life make the VEGASWING 61 vibrating level switch the ideal sensor for overflow and dry run protection, for example in storage tanks with cleaning agents. It can be used universally for all liquids and has the ability to detect the level reliably with millimetre accuracy, regardless of the mounting position.
VEGA has the right solution for every application. A complete overview of the VEGA portfolio for the pharmaceutical industry can be found here:
Related industries
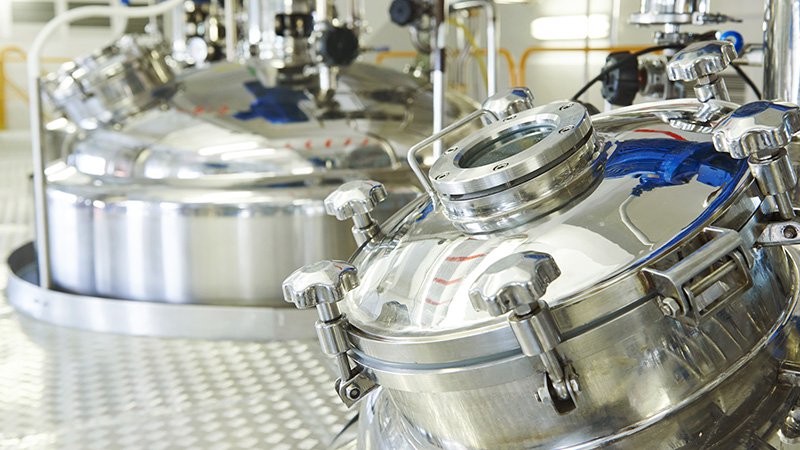
Pharmaceutical industry
Applications
CIP system - cleaning agent storage tanks
Level measurement and point level detection in the cleaning agent storage tank of the CIP system
In the pharmaceutical industry, cleaning of process equipment takes place within the framework of a validated "Clean in Place (CIP)" process to ensure aseptic conditions are maintained in production equipment, tanks and pipelines. Sodium hydroxide or concentrated acids are frequently used as cleaning agents, which are held in storage tanks within the CIP system. They are diluted in a premix vessel prior to use. Level measurement enables safe storage and optimal usage of these cleaning agents. Point level detection serves as overfill and dry run protection.
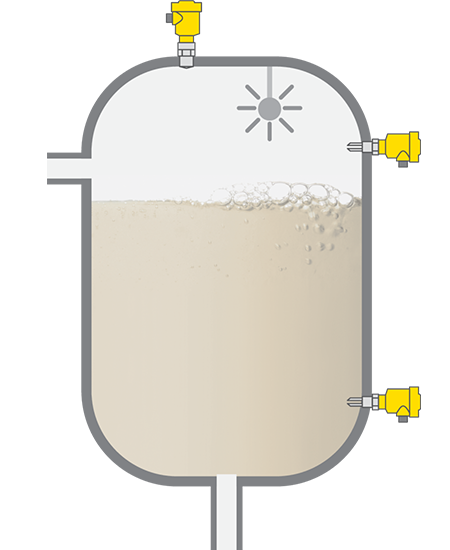
Reliable
Approved materials in compliance with FDA and EC 1935/2004
Cost effective
Maintenance-free operation
User friendly
Simple mounting
Capsule filling
Level and point level measurement during the capsule filling process
The empty raw capsules and the active ingredient pellets are stored above the filling machine. Reliable level measurement is required here to ensure a continuous supply to the process. The capsules are only lightly stuck together and can be easily sucked apart by a vacuum, so that the upper part separates from the lower part. The pellets are then filled into the lower part of the capsule. After filling, the capsules are transported to the collecting vessels via a hose system. A level detection system serves as overfill protection in these containers.
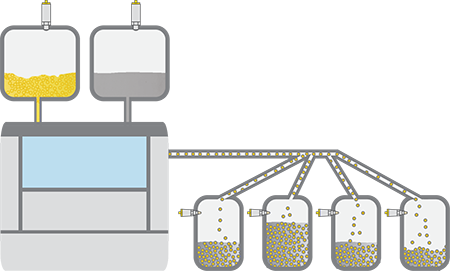
Reliable
Certified materials according to FDA and EC 1935/2004 regulations
Cost effective
Uninterrupted filling of the capsules thanks to reliable measurement
User friendly
Automatic filling through continuous monitoring of the containers
Bioreactor
Level and pressure measurement in the production of enzymes, proteins and antibodies
Some pharmaceutical companies use bioreactor vessels to cultivate particular cells or microorganisms required for certain treatments. The very high level of hygiene required means the vessels and all associated parts must be easy to thoroughly clean, because even the slightest contamination with other organisms can lead to an aborted production run. These reactors are mainly "batch-fed", where they are completely filled at the start and not emptied again until the process is completed. The pressure and level in the reactor have to be monitored continuously during process in order to obtain a high-quality yield.
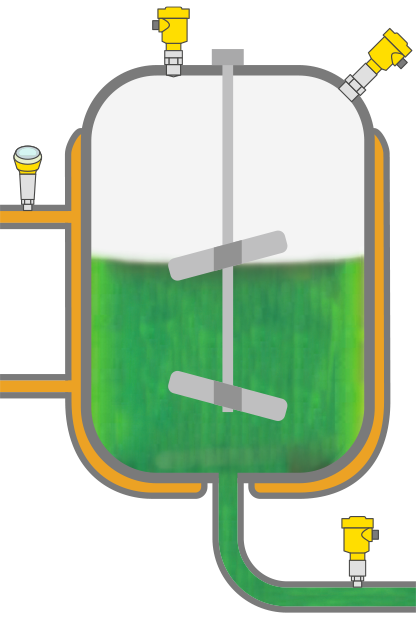
Reliable
Unaffected by extreme process conditions
Cost effective
Reliable, continuous operation with absolute hygiene
User friendly
Easy adjustment and setup, as internals do not interfere
Products
Export this article
Download as PDFShare this article
Comments ({{comments.length}})
{{getCommentAuthor(comment, "Anonymous")}} {{comment.timestamp | date : "dd.MM.yyyy HH:mm" }}
{{comment.comment}}