Precise radar measurement technology for fast processes
The motivation to continuously improve is very strong in some companies. The company Progroup, for example, is always interested in optimising its production processes simply because of the very dynamic situation in the packaging market. Although VEGAPULS 64 is only tiny component when compared to the huge paper machines, it was nevertheless decisive in the production optimisation process.
The mail-order business is booming, and along with it the market for corrugated paperboard packaging. Year after year, sales of corrugated paperboard, which is used to protect all kinds of goods for shipment, are increasing. Corrugated paperboard is the number 1 transport packaging material: two thirds of all shipped goods are sent in boxes made from it. Since most of the boxes are later recycled, this type of packaging is also environmentally friendly. Noticeable trend: The paperboard industry supplies increasingly complex corrugated paperboard products that conform closely with the wishes of the customer, such as customised transport packaging.
One company that has taken the partnership between customer and supplier to a new level is Progroup AG. Within the space of 25 years, the company has gone from zero to fourth place in the European corrugated paperboard market, producing corrugated base paper and creating new corrugated paperboard formats.
VEGAPULS 64 measures reliably even in small vessels
Smoothly functioning technologies are absolutely required to allow Progroup AG to supply its customers just in time. So the company always welcomes new ideas that have the potential to improve and speed up production processes. That is why, this time, the impulse for a special use of the then new VEGAPULS 64 at the Eisenhüttenstadt location came from the company’s own engineering team. The advantages of the non-contact radar level transmitter, for example
- its higher dynamics
- and better focussing,
were immediately recognised by the instrument specialists; after all, they knew the high quality of VEGA sensors ever since the plant started production in 2009. A large number of VEGA sensors were already in operation there. One feature in particular attracted the team’s attention right away, namely the ability of VEGAPULS 64 to reliably detect the level in very small vessels.
The level of the lubricating oil for the rotary lobe pumps is critical for their operation. Thanks to VEGAPULS 64, this level is now reliably monitored.
Estação de óleo hidráulico
Medição de nível e fluxo na estação de óleo hidráulico
Na seção de prensagem de uma máquina de papel, é necessário disponibilizar altas pressões para a drenagem. As estações de óleo sob pressão fornecem o óleo hidráulico necessário. Elas alimentam adicionalmente a lubrificação circulante, além de filtrar e resfriar o óleo. As bombas integradas transportam o óleo para as posições onde é necessário. Para o funcionamento automático da estação, é preciso medir o fluxo de óleo e o nível no tanque de armazenamento.
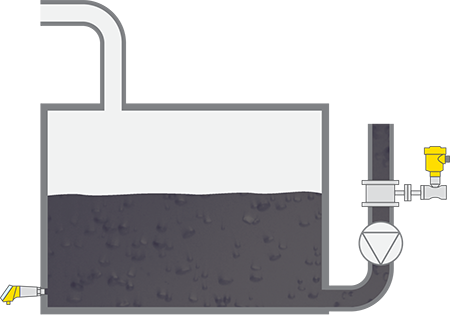
Seguro
Medição confiável para o funcionamento seguro da máquina de papel
Econômico
Transmissor de pressão diferencial com sonda de pressão dinâmica para uma medição de fluxo de óleo a baixos custos
Uso fácil
Leitura fácil do níveis de enchimento diretamente no ponto de medição
80 GHz makes level measurement easier and more precise in small tanks
More about the paper industry
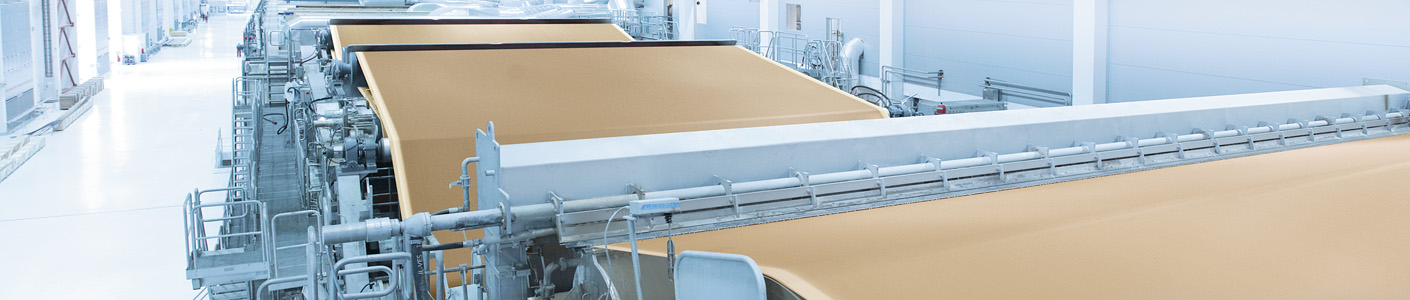
Indústria de papel
Products
Exportar este artigo
Baixar como PDFCompartilhar post
Comentários ({{comments.length}})
{{getCommentAuthor(comment, "Anônimo")}} {{comment.timestamp | date : "dd.MM.yyyy HH:mm" }}
{{comment.comment}}