New ultra-compact radar level sensor makes monitoring IBC inventory easy
When it comes to checking stocks in large silos and containers, radar measurement has long been the leading technology. But what about mobile containers like IBCs, whose contents are usually estimated with just a quick glance – if at all? VEGA has an impressive solution for this area of application: VEGAPULS Air. Thanks to radar technology, the miniature sensor delivers precise measured values and can be installed quickly and flexibly, as demonstrated by its use in a paper mill.
Paper, cardboard and paperboard are considered very inexpensive and light packaging materials. Nowadays, the majority of all cardboard products are now made from recycled waste paper. DS Smith is one of Europe's leading providers of sustainable packaging solutions, paper products and recycling services. Founded in 1657, the mill currently manufactures containerboard products (liner and medium grades) from 100 % waste paper. "We recycle about 400,000 tonnes of paper and cardboard every year and produce new paper from it. Our main customers then use the paper to produce boxes, trays and displays," explains Marco Verkerk, Coordinator of Technology & Product Support at the De Hoop plant, which is located on the outskirts of the Dutch municipality of Eerbeek. Not only does DS Smith focus on sustainability and environmental friendliness in production, the company is also constantly looking for ways to create packaging that uses less raw material.
Processes fine-tuned to each other
The basic production processes in paper recycling have hardly changed in the past few decades. Bales of waste paper are broken down into pulp in pulpers with the help of heated water and intensive pulverisation. Then all the impurities are removed from the pulp. The cleaned paper fibres eventually arrive at one of the two paper machines, where they are processed into new paper at a speed of 50 km/h. Customers use this paper to make cardboard boxes and trays. But the paper can also be used for the outer layers of plasterboard or the internals of a door.
At first glance, the processes look quite simple, but different raw materials have to be measured and added in with high precision. “That’s why there are several intermediate stages, where both solid and liquid ingredients and additives are fed into the process. This includes various liquids, which are introduced into the production process from standard IBCs of 1,000 litres each", explains Verkerk further. For more than ten years, the levels in the tanks and silos have been measured with VEGAPULS or VEGABAR level measuring instruments, which forward the measured values for processing in a PLC. Sensors like VEGAWELL, VEGASON and VEGADIF are also used at different locations in the plant. For example, on the paper machines, on pipelines with incoming raw and auxiliary materials and residual flows, as well as in the storage silos.
At first glance, the processes look quite simple, but different raw materials have to be measured and added in with high precision. “That’s why there are several intermediate stages, where both solid and liquid ingredients and additives are fed into the process. This includes various liquids, which are introduced into the production process from standard IBCs of 1,000 litres each", explains Verkerk further. For more than ten years, the levels in the tanks and silos have been measured with VEGAPULS or VEGABAR level measuring instruments, which forward the measured values for processing in a PLC. Sensors like VEGAWELL, VEGASON and VEGADIF are also used at different locations in the plant. For example, on the paper machines, on pipelines with incoming raw and auxiliary materials and residual flows, as well as in the storage silos.
How many different auxiliary materials are still stored in IBCs?
Brand new – VEGA’s newest measuring instrument has been operating successfully at the Dutch plant since July 2020. Three VEGAPULS Air 23 sensors were initially installed on the exchangeable IBCs on a trial basis. “We store more than 40 different chemicals and auxiliary materials in silos and IBCs. The fixed storage tanks and silos are already equipped with a level sensor connected to a PLC. The values are fed into our MBS programme to control the process. This way we know exactly what the consumption levels are like, so we can order raw materials to ensure that production continues without interruption", says Verkerk, describing the situation in his company.
With the mobile IBCs, however, this way of operating had not been possible. “Generally, we don’t need every auxiliary material for every type of finished product. So we drove through the plant every day to manually estimate the quantities in the IBCs", continues Verkerk, elaborating on the previous strategy. “Our experiences with the VEGA instruments we’ve used up to now have been very good. So, in September 2019, we asked VEGA if they had a solution for the IBCs. Unfortunately, the new instrument was still in the development phase", recalls Verkerk.
With the mobile IBCs, however, this way of operating had not been possible. “Generally, we don’t need every auxiliary material for every type of finished product. So we drove through the plant every day to manually estimate the quantities in the IBCs", continues Verkerk, elaborating on the previous strategy. “Our experiences with the VEGA instruments we’ve used up to now have been very good. So, in September 2019, we asked VEGA if they had a solution for the IBCs. Unfortunately, the new instrument was still in the development phase", recalls Verkerk.
Everything in view
It wasn’t until a few months later that the time had come: DS Smith De Hoop B.V. became the first company to monitor levels in IBCs with VEGAPULS Air 23. These wireless, autarkic sensors are inexpensive, flexible and reliable – and they quickly installed and easy to set up. During their development, energy efficiency was the main priority. Measurement performance, wireless data transmission and energy consumption had to be perfectly coordinated for this purpose. Batteries, in combination with optimised measurement cycles, provide the energy management that ensures a service life of up to 10 years. The sensors can be reliably used in a wide variety of scenarios wherever levels need to be measured, and thanks to adhesive adapters or flexible belt mounting, it make them very easy to attach to IBCs.
Due to the radar technology, measurement can be performed from the outside, so the IBC plastic tank doesn’t have to be opened or modified in any way. Installed in just a few simple steps, this solution can remain on the container permanently. The level of the liquid is transmitted regardless of where the IBC is located. The fixed measuring range is 1.2 m and the measurement/transmission interval 6 hours.
Even when the containers are stacked on top of each other, the VEGA sensor on each individual container records the current level and its location several times a day – and transmits this data wirelessly to the cloud. This capability makes the new instruments virtually predestined for use in IoT applications. The measured values from the sensors can also be transmitted via mobile network (NB-IoT/LTE-M1) to VEGA Inventory System.
Due to the radar technology, measurement can be performed from the outside, so the IBC plastic tank doesn’t have to be opened or modified in any way. Installed in just a few simple steps, this solution can remain on the container permanently. The level of the liquid is transmitted regardless of where the IBC is located. The fixed measuring range is 1.2 m and the measurement/transmission interval 6 hours.
Even when the containers are stacked on top of each other, the VEGA sensor on each individual container records the current level and its location several times a day – and transmits this data wirelessly to the cloud. This capability makes the new instruments virtually predestined for use in IoT applications. The measured values from the sensors can also be transmitted via mobile network (NB-IoT/LTE-M1) to VEGA Inventory System.
Quick setup and commissioning
Initially, three IBCs in the plant were equipped with VEGAPULS Air 23. Installation was really simple: remove the protective film, stick the sensor on, it's done. Thanks to 80-GHz radar technology, VEGAPULS Air, with its water-tight, plastic encapsulated antenna, it can measure the level right through the plastic top of the IBC. “We had previously considered whether we could get along with a wire-connected radar instrument. But at the locations where the IBCs are deployed, connecting with cables was extremely difficult and the time savings would not have offset the investment costs", Verkerk makes clear.
No approvals or process fittings were required for the installation of VEGAPULS Air. Since the instrument measures down through the container roof from the outside, it doesn’t need to employ especially high resistance materials to chemicals. It doesn’t matter what medium is inside the IBC. Another big advantage: the IBC can be rigorously cleaned on the outside, as the sensors have IP68 and IP69K protection.
No approvals or process fittings were required for the installation of VEGAPULS Air. Since the instrument measures down through the container roof from the outside, it doesn’t need to employ especially high resistance materials to chemicals. It doesn’t matter what medium is inside the IBC. Another big advantage: the IBC can be rigorously cleaned on the outside, as the sensors have IP68 and IP69K protection.
Experiences as a first user
“We were among the first to use the new instrument and thus experience how it really works in practice", says Verkerk. In his opinion, double-sided adhesive tape is sufficient for attaching the sensor to the IBC. “Once, in the course of an IBC replacement, we forgot to remove the adhesive on the sensor and mount it on the new IBC. We found it a week later lying on the forklift", he recalls with a laugh. But the sensor wasn’t bothered by this mishap. As soon as it was glued back onto the correct IBC, it started delivering correct readings immediately.
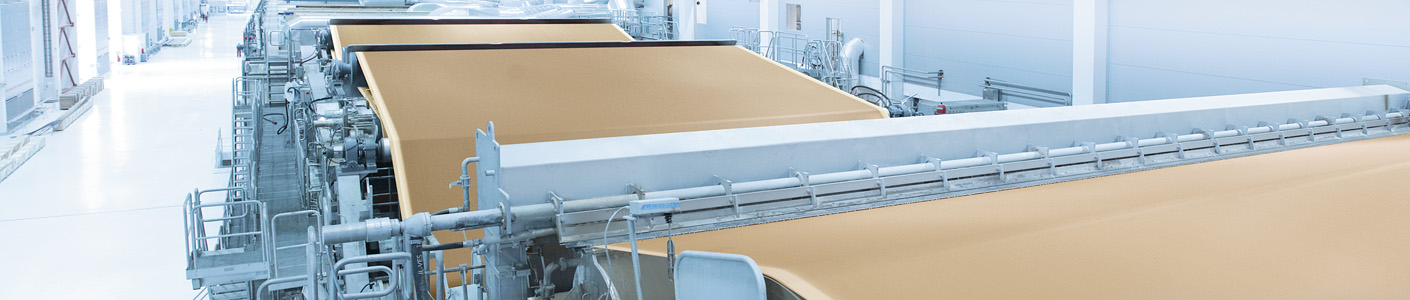
Бумажная промышленность
Прочные, стабильные и удобные в обслуживании датчики для бумажной промышленности.
Для промышленности
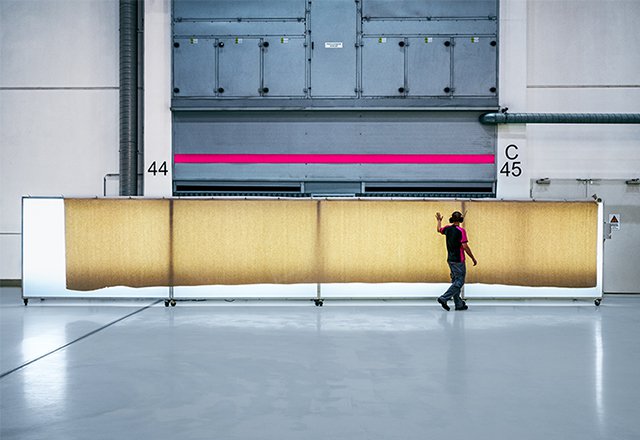
Precise radar measurement technology for fast processes
читать дальшеЭкспортировать эту статью
Скачать как PDFПоделиться этой статьей
Комментарии ({{comments.length}})
У этой статьи еще нет комментариев. Напишите сейчас первый комментарий!
{{getCommentAuthor(comment, "Анонимный")}} {{comment.timestamp | date : "dd.MM.yyyy HH:mm" }}
{{comment.comment}}
Написать комментарий
Это поле обязательно для заполнения
Это поле обязательно для заполнения
Это поле обязательно для заполнения
Неверный адрес e-mail
Это поле обязательно для заполнения
Your comment must not contain any links or email addresses
Это поле обязательно для заполнения
Неверная капча
Произошла ошибка. Пожалуйста, попытайтесь еще раз.